Industrial oil treatment systems are designed to purify, condition, and rejuvenate oils used in various industrial applications, particularly in machinery, equipment, and transformers. These systems help extend the life of the oil, improve the performance of equipment, and reduce downtime and maintenance costs. Below are the common types of industrial oil treatment systems and their functions:
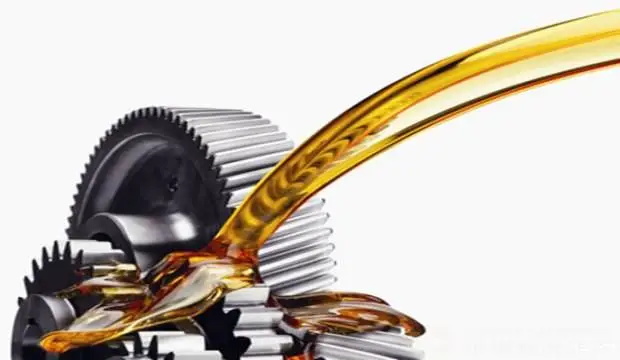
1. Transformer Oil Treatment Systems
Transformer oil treatment systems are used to purify insulating oils in transformers. These systems primarily remove contaminants such as moisture, gases, particulate matter, and oxidation products.
Key Processes:
- Vacuum Dehydration: Removes moisture from the transformer oil using a vacuum and heating process.
- Vacuum Degassing: Removes dissolved gases like nitrogen, oxygen, and CO₂ from the oil.
- Particle Filtration: Removes solid contaminants from the oil through filtration.
- Acid Removal: Some systems use special filtering or treatment methods to remove acids or oxidation products from the oil.
Common Equipment:
- High-Vacuum Oil Purifiers: Used for large-scale transformer oil treatment, applying a high vacuum to remove moisture and gases.
- Offline Oil Filtration Units: Used for periodic oil treatment in transformers, circulating the oil outside the transformer for cleaning.
- Portable Oil Purifiers: These mobile units are used for onsite oil treatment, especially in the case of mobile transformers or equipment in the field.
2. Oil Filtration and Purification Systems
These systems are used in various industries where oils such as hydraulic, lubrication, and gear oils require periodic cleaning to maintain their effectiveness.
Key Processes:
- Filtration: The primary method used to remove particles and solid contaminants from oils, typically through micron filters, depth filters, or activated carbon filters.
- Centrifugal Separation: Some systems use centrifugal force to separate water and particulate matter from oil.
- Heat Treatment: This is sometimes used alongside filtration to reduce the viscosity of oil or aid in the removal of contaminants.
- Dehydration: Removes free water from oils through filtration or centrifugal separation.
- Decontamination: Using various methods such as electrostatic separation, oxidation, or chemical treatments to remove dissolved contaminants.
Common Applications:
- Hydraulic Oil Systems: To extend the life of hydraulic oils by removing solid contaminants and moisture.
- Lubrication Systems: In engines, turbines, and compressors, where oil cleanliness is critical to preventing wear and tear.
- Gear Oil Systems: In industrial machinery and power transmission systems where gears operate under high stress and heat.
3. Oil Regeneration Systems
Oil regeneration systems are more advanced treatment processes that not only purify but also rejuvenate used oils by removing oxidation products, acids, and other contaminants that degrade oil quality.
Key Processes:
- Clay Filtering: Involves passing used oil through activated clay or Fuller’s earth, which adsorbs contaminants like acids, oxidation by-products, and colorants.
- Activated Carbon Treatment: Activated carbon is used to remove dissolved contaminants like dissolved gases, volatile organic compounds (VOCs), and color bodies.
- Vacuum Distillation: A method used to remove water, low-boiling contaminants, and light fractions from oils, while restoring the oil's viscosity.
- Resins and Chemical Treatment: Some systems use resins or chemical additives to remove specific contaminants or improve the oil's performance.
Common Applications:
- Lubricating Oils: To extend the life of oils in machines and engines by removing impurities that cause oxidation and breakdown.
- Hydraulic Oils: Extending the life of hydraulic systems by treating oils to reduce wear and maintain efficiency.
4. Centrifugal Oil Purification Systems
Centrifugal oil purifiers use the principle of centrifugal force to separate contaminants from oils. These systems are typically used for removing water and solid particles from oils.
Key Processes:
- Centrifugal Separation: Oils are spun at high speeds, causing the denser contaminants (such as water and solids) to separate from the oil.
- Continuous Operation: These systems typically operate continuously, keeping the oil clean during its usage.
- Pre-Treatment: Some centrifugal units require pre-filtering or heating of the oil before it enters the centrifuge to improve separation efficiency.
Common Applications:
- Marine and Ship Engines: These systems are often used in the marine industry to purify lubricating oils in engine and transmission systems.
- Heavy Industry Equipment: Used to maintain oil quality in large industrial equipment like compressors, turbines, and generators.
5. Electrostatic Oil Purifiers
Electrostatic oil purification systems use electrical fields to remove particles and water from oils. The electrostatic charge attracts contaminants, which are then removed through filtration or separation.
Key Processes:
- Electrostatic Precipitation: Oil is passed through an electrostatic field that charges the particles, causing them to migrate to a collection plate.
- Water Separation: Some systems can also remove water droplets from oil by using electrostatic forces to cause phase separation.
Common Applications:
- Hydraulic Systems: To maintain clean oil in hydraulic systems, preventing the wear of components.
- Lubrication Systems: In high-precision industrial machinery, such as turbines, compressors, and gearboxes, where oil cleanliness is crucial for preventing wear and tear.
6. Oil Degassing Systems
Oil degassing systems are primarily used to remove dissolved gases from insulating oils, such as in transformers and other electrical equipment.
Key Processes:
- Vacuum Degassing: The oil is subjected to a vacuum, which causes dissolved gases to come out of solution and be removed from the oil.
- Gas Separation: Using methods such as sparging (passing gas through the oil) to separate dissolved gases from the oil.
Common Applications:
- Transformer Oil: To remove gases like nitrogen, oxygen, hydrogen, and CO₂, which can degrade the oil’s dielectric strength.
- Power Generators and Large Motors: In power generation plants, where oil used for lubrication and cooling can accumulate gases that affect performance.
7. Coalescing Oil Water Separators
These systems are used to remove water from oils in systems where oil and water may become emulsified.
Key Processes:
- Coalescence: Emulsified water droplets in oil are made to coalesce (combine) into larger droplets, which can then be easily separated.
- Separation: The coalesced water is removed from the oil, which is then returned to the system.
Common Applications:
- Industrial Lubrication Systems: To prevent water contamination in oils used in manufacturing machinery, where water ingress could cause rusting or degradation.
- Power Plants: In systems that use oil for cooling or lubrication, where water contamination can affect performance.
8. Filtration and Oil Conditioning Systems for Food and Beverage Industry
In industries such as food processing and pharmaceuticals, where oils are used in production lines, special filtration and treatment systems are used to remove contaminants while preserving the oil's quality and safety.
Key Processes:
- Micron Filtration: Fine filtration techniques to remove micro-sized particles and impurities.
- Deodorization: Used in edible oil production to remove off-flavors and odors from oils.
Common Applications:
- Cooking Oils: For removing contaminants in edible oils used in food production.
- Pharmaceuticals: Where oils are used in certain production processes, requiring highly refined and purified oils.
Conclusion
Industrial oil treatment systems are vital to ensuring that oils used in machinery, transformers, and various processes remain clean and efficient. By utilizing advanced techniques like vacuum dehydration, filtration, centrifugal separation, and chemical treatment, these systems help to extend the life of the oils, improve the reliability of equipment, and reduce operational costs. Each type of system is tailored to specific needs, whether it’s for transformer oil, hydraulic systems, or lubrication applications.