Transformer oil filtration is a critical process to ensure the longevity and efficient operation of transformers by removing contaminants such as moisture, gases, and particulate matter from the insulating oil. Here's a detailed look at the transformer oil filtration process:
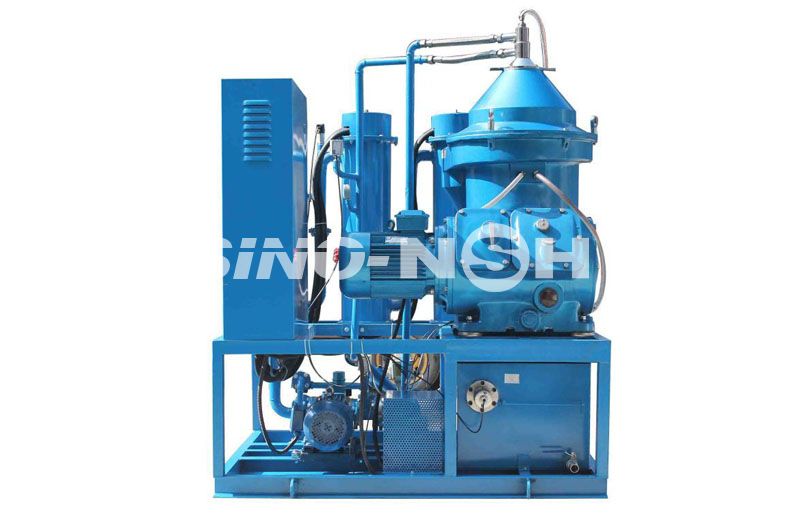
1. Pre-Filtration (Initial Assessment)
Before filtration begins, a thorough assessment of the oil is conducted to determine the type and extent of contamination. Common contaminants include:
- Water: Dissolved or free water.
- Gases: Acids, CO₂, CO, and other dissolved gases.
- Particulates: Dirt, metal particles, carbon residues, etc.
- Oxidation By-products: Acidic compounds formed due to oil degradation.
This assessment helps in choosing the right filtration process and equipment.
2. Vacuum Dehydration (Water Removal)
One of the most critical aspects of oil filtration is the removal of water. This process is usually done in a high vacuum transformer oil purifier. The main steps include:
- Heating: The transformer oil is heated to a temperature (around 50-80°C) to increase the evaporation rate of water.
- Vacuum Application: A vacuum is applied to the system to reduce the boiling point of water and allow the moisture to evaporate even at lower temperatures.
- Condensation: The moisture vapor is then condensed and separated from the oil.
This process is essential because excess water in transformer oil can lead to reduced insulating properties, leading to transformer failure.
3. Vacuum Degassing (Gas Removal)
In addition to moisture, transformer oil can also contain dissolved gases such as nitrogen, oxygen, hydrogen, and carbon dioxide. These gases can affect the insulating properties of the oil and contribute to breakdowns.
The process involves:
- Vacuum Treatment: The oil is subjected to a high vacuum that helps release the dissolved gases from the oil.
- Gas Separation: The dissolved gases are separated and expelled from the system, ensuring the oil remains pure.
4. Filtration (Particle Removal)
After moisture and gases are removed, the oil may still contain particles such as dirt, dust, and metallic contaminants. Filtration ensures that the oil is free from these particulates.
- Micron Filtration: Special filters with fine mesh or filtration media are used to trap particles as small as a few microns.
- Advanced Filters: Some systems use activated carbon or cellulose-based filters that also help absorb contaminants like acids or oxidation by-products.
5. Polishing (Final Purification)
This step involves passing the oil through a polishing filter to ensure it’s free from any remaining small contaminants that could affect the performance of the transformer. The goal is to ensure the oil has minimal impurities, maintaining its high dielectric strength.
6. Cooling
After the oil has been purified, it is cooled back to its normal operating temperature before being reintroduced into the transformer. The cooling process also ensures that any changes in the oil's viscosity due to heating are mitigated.
7. Reintroduction into Transformer
Once the oil has been purified and tested for quality (e.g., dielectric strength, moisture content, gas levels, and particle concentration), it is returned to the transformer tank, replacing the old contaminated oil.
Types of Oil Filtration Systems
There are different types of oil filtration systems used in the process, each suited for specific requirements:
- Portable Vacuum Oil Purifiers: These are used for on-site purification and are often mobile, making them easy to transport to different transformer locations.
- Continuous Oil Purification Systems: These are integrated into transformer substations and can continuously filter oil without the need for frequent oil changes.
- Offline Filtration Systems: These systems work by circulating the oil outside the transformer in a closed-loop system where it is filtered before being returned.
Benefits of Transformer Oil Filtration
- Improved Insulation: Clean oil has better-insulating properties, reducing the risk of electrical failure.
- Increased Transformer Life: Regular oil filtration removes contaminants that can cause internal damage to the transformer, extending its service life.
- Reduced Risk of Failure: Moisture and particulate buildup in the oil can lead to short circuits or transformer overheating. Filtration mitigates these risks.
- Cost Savings: By maintaining oil quality, transformer maintenance and repair costs are reduced, and the need for full oil replacement is minimized.
Testing After Filtration
After the filtration process, the oil should be tested for:
- Dielectric Strength: To measure the oil’s ability to resist electrical breakdown.
- Moisture Content: To ensure the oil is sufficiently dry.
- Acidity and Contaminants: Testing for oxidation by-products and particulate content is also important.
Regular transformer oil filtration is an essential aspect of transformer maintenance to keep the transformer running efficiently and avoid costly failures.