Choosing the right turbine oil purification system is critical to ensuring the efficiency, longevity, and reliability of turbine machinery. Turbine oils, especially in steam and gas turbines, play a vital role in lubrication, cooling, and cleaning internal components. Over time, these oils become contaminated with water, particulates, and oxidation products, which can degrade performance and cause equipment failure if not properly treated.
Here’s a guide to help you select the most suitable turbine oil purification system for your needs:
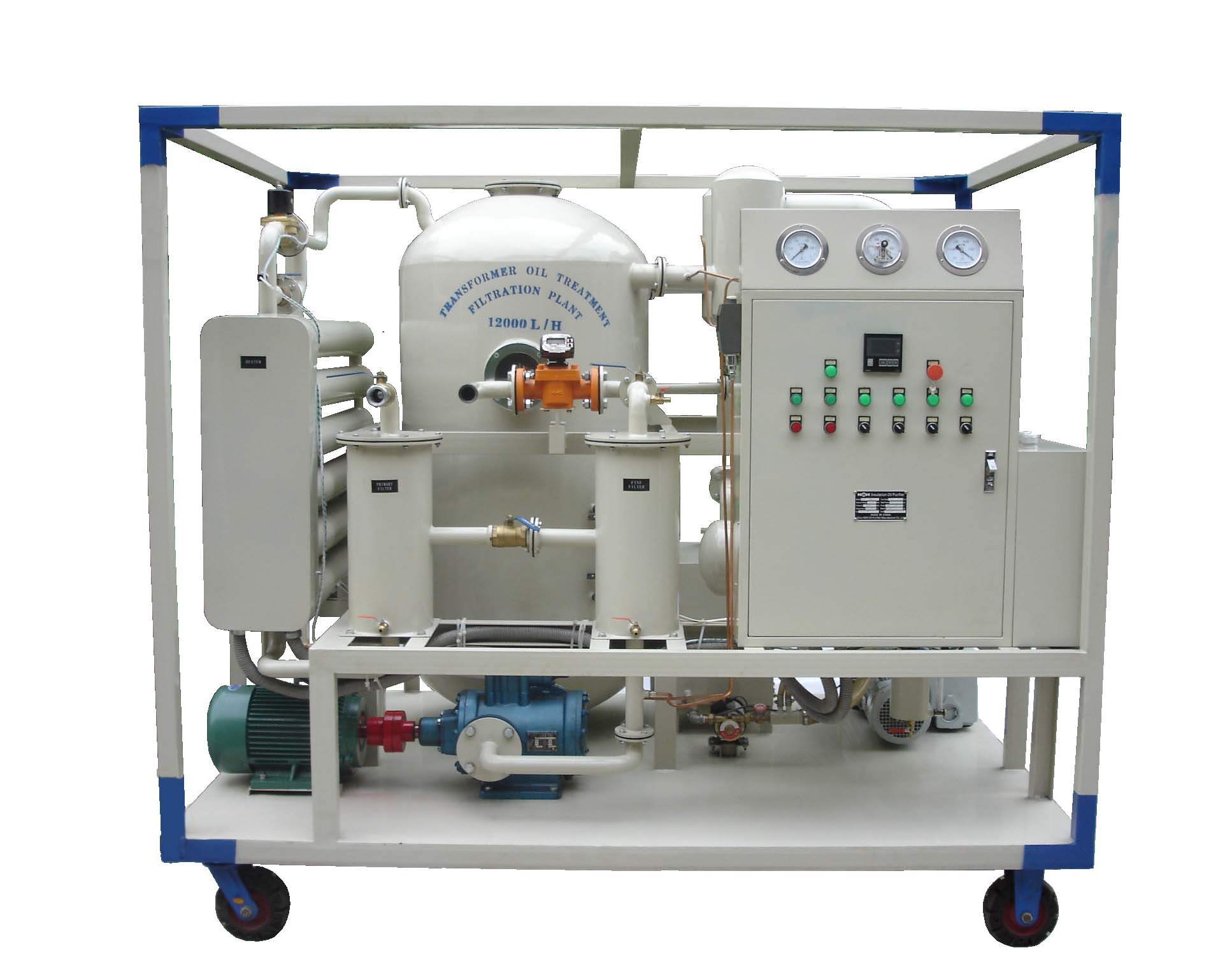
1. Understand the Specific Contaminants in the Oil
Turbine oils are susceptible to contamination by:
- Water (both free water and emulsified water).
- Solid Particles (dirt, rust, carbon, and metal wear particles).
- Oxidation Products (acids, varnish, and sludge).
- Gases (air or dissolved gases like nitrogen, oxygen, and hydrogen).
The system you choose must be capable of addressing the primary contaminants present in your turbine oil.
2. Determine the Capacity and Flow Rate Requirements
- Oil Volume: The system should be able to handle the total volume of oil in the turbine system, including the oil reservoir and any associated piping.
- Flow Rate: The purification system should match or exceed the required flow rate for effective treatment. It needs to treat oil without causing delays or bottlenecks in the operation of the turbine.
- Turnaround Time: Systems designed for continuous operation might have slower treatment rates but offer long-term efficiency. If you need rapid purification, batch-type systems might be more appropriate.
3. Choose the Type of Purification System
There are several types of turbine oil purification systems, each with different capabilities:
a. Vacuum Dehydration and Degassing Systems
- Purpose: These systems are effective at removing moisture and dissolved gases from the turbine oil.
- Working Principle: Oil is heated, and then a vacuum is applied to lower the boiling point of water and allow it to evaporate. The system also removes dissolved gases, improving the oil’s dielectric strength.
- Best for: Turbine oils that are contaminated primarily with water and gases.
- Benefits: Prevents corrosion and rusting of turbine components by removing water; improves oil insulating properties.
- Example: High-vacuum oil purifiers.
b. Centrifugal Oil Purifiers
- Purpose: These systems are designed to remove solid particulates from turbine oils.
- Working Principle: Centrifugal force separates water and solid particles from the oil. These systems are effective for removing large particulates and emulsified water.
- Best for: Turbine oils contaminated with large amounts of particulate matter and free water.
- Benefits: Efficient at separating dense particles; reduces wear and tear on turbine components.
- Example: Decanter centrifuges or centrifugal separators.
c. Filtration Systems
- Purpose: Filtration systems use fine mesh or filter media to remove solid particles from the oil, including dirt, wear particles, and oxidation products.
- Working Principle: The oil is passed through filter elements that trap contaminants based on size and other properties.
- Best for: Turbine oils with high levels of particulate contamination.
- Benefits: Can improve oil cleanliness and extend the life of the turbine.
- Types: Micron filters, depth filters, and electrostatic filters.
d. Resin-based Oil Treatment Systems
- Purpose: These systems use resin to remove oxidation products such as acids and varnish-forming materials.
- Working Principle: Resin-based filters absorb contaminants like acidic compounds, carbon, and varnish precursors that accumulate in turbine oils.
- Best for: Turbine oils experiencing oxidation and varnish buildup, especially in older turbines.
- Benefits: Prevents varnish formation, which can clog oil passages and damage components.
- Example: Resin-based filtration systems.
e. Electrostatic Oil Purifiers
- Purpose: Electrostatic purification systems remove fine particulate contaminants and water droplets using electrostatic forces.
- Working Principle: The oil is exposed to an electrostatic field, which causes contaminants to be attracted to collection plates for removal.
- Best for: Oil that is contaminated with very fine particles or small amounts of emulsified water.
- Benefits: Efficient for continuous cleaning with minimal oil loss.
- Example: Electrostatic oil separators.
4. Consider Oil Condition Monitoring
- Online Monitoring: Some turbine oil purifiers come with online sensors and monitoring capabilities, allowing you to track the condition of the oil in real time (e.g., water content, particle count, and acidity).
- Automation: Look for systems that can automatically shut down or adjust the treatment process when the oil reaches specific contamination levels. Automated systems improve efficiency and reduce the need for manual intervention.
5. Energy Efficiency
- Power Consumption: Some purification systems, like high-vacuum units, can consume a significant amount of energy. When choosing a system, it’s essential to evaluate its energy efficiency and operational cost.
- Operational Costs: Beyond the initial purchase cost, consider the system’s maintenance requirements and the cost of consumables such as filters, resins, or heating elements.
6. Maintenance and Service Requirements
- Ease of Maintenance: Choose a system that’s easy to maintain, with readily available spare parts and service options.
- Scheduled Maintenance: Look for systems that offer predictive maintenance capabilities (e.g., filters and resin replacement based on operational hours or oil condition).
- Durability and Reliability: Opt for systems that are built to withstand harsh industrial environments and require minimal downtime.
7. Environmental Considerations
- Waste Disposal: Some purification systems generate waste (e.g., spent filters, sludge, resin, or used oils). Choose a system that complies with local environmental regulations for waste disposal.
- Emissions: Some vacuum-based systems might release volatile organic compounds (VOCs) during operation. Make sure that any system you choose has adequate emission control features if required.
8. System Integration
- Compatibility: Ensure the purification system is compatible with your turbine’s oil circulation system (flow rate, temperature, pressure, etc.).
- Automation: If your turbine operates in a highly automated environment, you may prefer a system that integrates with your central control system for monitoring and adjustments.
- Size and Footprint: Choose a system that fits into your facility's layout, with space for future expansion if required.
9. Cost vs. Benefit Analysis
- Initial Cost: Consider the upfront purchase cost of the system.
- Long-Term Value: Evaluate the system's efficiency, energy consumption, and the cost savings it provides in terms of reducing maintenance costs, extending oil life, and improving turbine performance.
- ROI: Calculate the return on investment by considering the operational savings from fewer oil changes, reduced turbine maintenance, and extended service life of both the oil and turbine.
Conclusion
When selecting a turbine oil purification system, it is essential to consider factors such as the type of contaminants (water, solids, gases, or oxidation products), the capacity and flow rate requirements, and the specific purification technology best suited for your turbine oil’s condition. Consider the maintenance needs, cost-effectiveness, environmental impact, and system integration to ensure that the system operates efficiently and enhances the life of both your oil and turbine machinery.
Taking a holistic approach will help you select a system that optimizes your turbine's performance, reduces downtime, and lowers overall operational costs.