Filtering transformer waste oil is essential to remove contaminants such as dirt, sludge, carbon, moisture, acids, and other by-products accumulated during the transformer’s operation. This process helps restore the oil to a usable condition, improving its insulating properties and extending the life of the transformer. Waste oil treatment typically involves a combination of physical and chemical processes to purify and regenerate the oil. Below are the steps involved in filtering transformer waste oil:
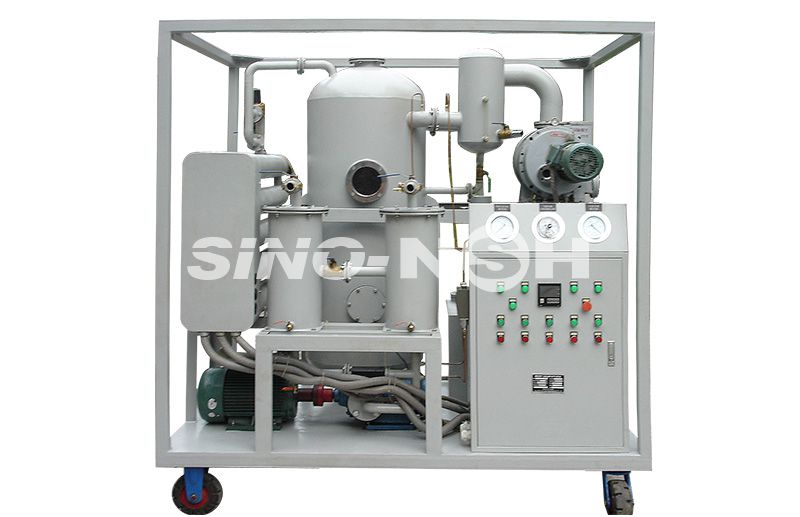
1. Preliminary Separation (Settling and Decanting)
- Purpose: Remove large solid particles, water, and heavy sludge from the waste oil before more advanced filtration.
- Process:
- The oil is left to settle in a tank for several hours or days, allowing heavy particles, water, and sludge to naturally separate from the oil.
- The water and sludge can then be decanted or drained from the bottom of the tank. This is a relatively simple step but may not remove finer particles or dissolved contaminants.
2. Mechanical Filtration
- Purpose: Remove large solid contaminants (dirt, dust, and sludge).
- Process:
- Waste oil is passed through mechanical filters such as mesh, paper filters, or cartridge filters.
- These filters capture larger particulate matter but may not be effective for very fine particles or dissolved contaminants. Typically, filters with different mesh sizes are used for sequential filtration to capture progressively smaller particles.
Types of mechanical filters:
- Mesh filters: Used for larger particulates.
- Cellulose or paper filters: Can trap fine particulates and some moisture.
- Cartridge filters: Often used for more thorough filtration of fine particles.
3. Vacuum Dehydration (Moisture Removal)
- Purpose: Remove water (both free and dissolved) from the oil.
- Process:
- Waste oil is heated to a specific temperature (around 60–80°C) and then passed through a vacuum chamber.
- The vacuum reduces the boiling point of water, causing the moisture to evaporate. This water is then extracted from the system using a condenser and moisture collection unit.
- Dehydration is critical because moisture can degrade the oil's insulating properties and promote corrosion within the transformer.
Additional Methods for Moisture Removal:
- Silica Gel or Molecular Sieves: Can be used to absorb trace amounts of water that might remain after vacuum dehydration.
- Centrifuges: High-speed centrifuges can be used to separate free water from the oil.
4. Degasification (Gas Removal)
- Purpose: Remove dissolved gases, including hydrogen, methane, carbon dioxide, and other by-products of electrical activity or oil degradation.
- Process:
- The oil is heated in a vacuum, allowing dissolved gases to escape and be evacuated.
- Vacuum degasification ensures that the oil's dielectric properties are not compromised by the presence of dissolved gases, which can cause electrical discharges or partial discharges in the transformer.
5. Acid Removal (Neutralization and Deacidification)
- Purpose: Neutralize acids and remove oxidation products that can harm the oil and reduce its performance.
- Process:
- The waste oil may contain acids (such as sulfuric acid or other organic acids) formed due to oxidation over time. These acids need to be neutralized to prevent them from corroding transformer parts.
- Chemical Neutralization: Neutralizing agents, like sodium hydroxide (caustic soda), can be added to the oil to neutralize acids.
- Activated Clay or Fuller’s Earth Treatment: Another method involves using activated clay (Fuller’s Earth) to adsorb acid compounds and oxidation products. This process helps restore the oil’s properties.
6. Fine Filtration (Polishing)
- Purpose: Remove fine particulate matter and impurities that cannot be captured through earlier filtration stages.
- Process:
- The oil is passed through a fine filter, such as activated carbon or diatomaceous earth, which adsorbs fine particles and residual contaminants. This process also helps improve the clarity of the oil.
- Activated Carbon: Can remove trace amounts of dissolved gases, odors, and oxidation products.
- Diatomaceous Earth: Often used for polishing and further refining oil to improve its quality.
7. Regeneration (If Needed)
- Purpose: Regenerate highly degraded oil, especially if it has been in service for a long period and is heavily contaminated.
- Process:
- Regeneration can be achieved by passing the waste oil through Fuller’s Earth or a similar regenerative material. This process adsorbs polar compounds (such as oxidized oils and acids) and restores the oil’s insulating properties.
- Regeneration via High-Temperature Heating: In some cases, the oil may be subjected to high temperatures in the presence of an adsorbent material, allowing for the removal of carbon and oxidation products that impair the oil’s performance.
8. Final Testing and Quality Control
- Purpose: Ensure the treated oil meets all required standards for transformer operation.
- Process:
- Breakdown voltage test to determine the oil's insulating strength.
- Moisture content test (typically under 30 ppm).
- Acidity testing to ensure the oil is neutralized (acidity should be under 0.03 mg KOH/g).
- Gas analysis to check for dissolved gases, confirming their removal.
- Flash point testing to ensure the oil is safe and stable.
The oil must pass these tests to ensure that it will function effectively in the transformer.
9. Oil Refilling or Disposal
- Once the oil is filtered, treated, and tested, it can be reused by refilling it back into the transformer or disposed of if it’s no longer viable for reuse.
Equipment Used in Transformer Oil Filtration:
- Vacuum dehydrators: For moisture and gas removal.
- Filtration units: For solid particle removal (mesh, paper, and cartridge filters).
- Centrifuges: For separating water from the oil.
- Fuller’s Earth or Activated Clay filters: For regeneration and acid removal.
- Polishing filters: For final filtration and clarifying.
Environmental Considerations:
- Waste Disposal: After the oil treatment process, contaminants such as water, sludge, acids, and gases must be disposed of properly. Special care should be taken to follow environmental regulations for hazardous waste disposal.
- Recycling: If the oil is deemed too degraded to be reused, it may be recycled through specialized facilities that can process used transformer oil safely.
By following these steps, transformer waste oil can be filtered, purified, and potentially regenerated to restore its insulating properties, which reduces the need for new oil and promotes environmental sustainability.