Factory transformer oil treatment methods are designed to restore and maintain the quality of transformer oil, ensuring that it continues to provide optimal insulation and cooling properties for transformers. These methods are typically employed during the manufacture, initial filling, or when oil is changed or reconditioned at a factory setting. The treatment process typically combines several steps to ensure the oil meets the necessary specifications for optimal performance.
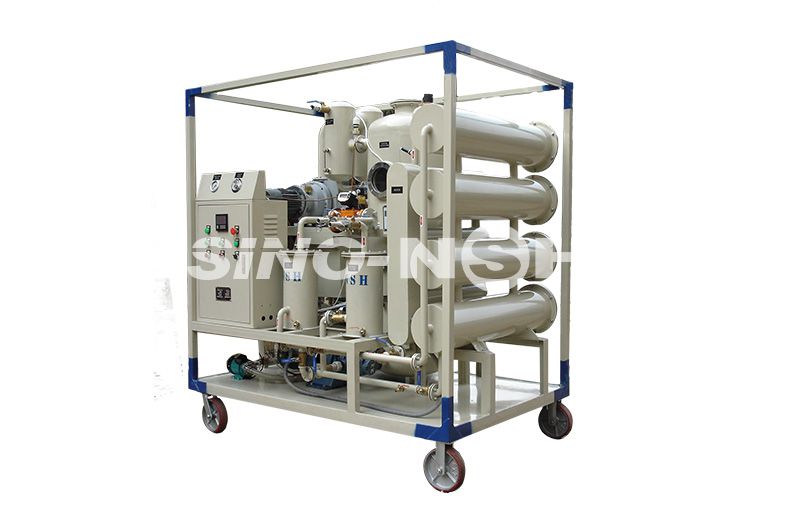
Key Steps in the Factory Transformer Oil Treatment Method:
1. Oil Filtration
- Purpose: Remove solid particulates, sludge, and other physical contaminants from the oil.
- Process: The oil is passed through a filtration system, which can include paper, mesh, or other types of filtration media to trap dirt, dust, and solid particles. This step ensures the oil is free from contaminants that could damage transformer components.
2. Dehydration (Moisture Removal)
- Purpose: Remove water from the oil, as water can significantly degrade the dielectric strength of the oil and lead to oxidation.
- Process: The oil is heated to a controlled temperature (typically between 60–80°C), and a vacuum system is applied. The vacuum helps remove moisture by evaporating the water, which is then condensed and removed from the system. In some cases, dehydrating agents such as silica gel or molecular sieves are used to absorb residual moisture.
3. Degasification (Gas Removal)
- Purpose: Remove dissolved gases like hydrogen, methane, and carbon dioxide that can accumulate in the oil due to electrical arcing or long-term transformer operation.
- Process: The oil is subjected to a vacuum or partial vacuum while being heated to release dissolved gases. These gases are then evacuated, restoring the oil's dielectric properties.
4. Acid Removal (Deacidification)
- Purpose: Remove acidic compounds (mainly due to oxidation) that can reduce the insulating ability of the oil and cause corrosion in transformer components.
- Process: Chemical agents or adsorbents, such as sodium hydroxide (caustic soda) or specific ion-exchange resins, can be added to neutralize the acids. Alternatively, some purification systems use active clays or other adsorbents to remove acidic substances.
5. Oil Polishing (Optional)
- Purpose: Further improve the clarity and purity of the oil, removing fine contaminants that may not have been eliminated during previous steps.
- Process: Oil is passed through activated carbon filters, which help remove trace impurities, color, and odor, ensuring the oil meets high-quality standards.
6. Oil Regeneration (If Required)
- Purpose: Restore the oil's properties, especially if the oil has undergone significant degradation due to prolonged use.
- Process: This step may involve adding additives to the oil to rejuvenate its properties. Common additives include antioxidants, corrosion inhibitors, or metal passivators. In some cases, more advanced treatment processes like using fuller’s earth or clay for regeneration are employed to remove dissolved polar compounds that can affect the oil’s performance.
7. Final Testing and Quality Control
- Purpose: Ensure that the oil meets all required specifications before it is used in a transformer.
- Process: The oil undergoes rigorous testing, including:
- Breakdown voltage testing to determine dielectric strength.
- Moisture content analysis to ensure water is within acceptable limits (typically less than 30 ppm).
- Acidity testing to ensure acid levels are within allowable limits (less than 0.03 mg KOH/g).
- Gas analysis to check for dissolved gases and confirm their removal.
- Flash point testing to check for safety.
8. Oil Filling
- Purpose: Once the oil has been purified and tested, it is used to fill the transformer.
- Process: The purified oil is carefully transferred into the transformer under controlled conditions, ensuring that the oil is free from air bubbles and that no contamination occurs during the filling process.
Methods Used for Transformer Oil Treatment in Factories:
Offline (Static) Treatment Systems: In a factory setting, oil treatment often takes place in offline (static) systems where the oil is drained and processed in dedicated units before being returned to the transformer. These systems may include vacuum dehydrators, filtration units, and degasification tanks.
Online (Dynamic) Treatment Systems: In some factories, especially those producing transformers in bulk, online treatment methods can be used. These systems allow the oil to be treated while the transformer is being filled or during initial commissioning.
Clay Treatment (Fuller’s Earth): Sometimes, a fuller’s earth clay treatment is used for oil regeneration. This method involves passing the oil through activated clay, which adsorbs polar impurities, such as oxidation products, improving the overall quality and insulating properties of the oil.
Final Considerations:
Environmental and Safety Aspects: Oil treatment processes must be designed with environmental concerns in mind. Contaminants, such as acids and gases, need to be properly neutralized or disposed of to meet environmental regulations. Furthermore, the handling of transformer oil must comply with safety standards to avoid exposure to potentially hazardous materials, particularly during the heating or vacuum processes.
Cost and Efficiency: The treatment process can vary in complexity and cost depending on the transformer size, the condition of the oil, and the equipment used. Factory treatment methods aim to balance efficiency and cost-effectiveness while maintaining high-quality oil for transformers.
By using these methods, transformer manufacturers ensure that the oil used in transformers is clean, dry, and free of contaminants, which maximizes the transformer’s performance, reliability, and lifespan.