The turbine oil purification process is designed to restore and maintain the quality of oil used in steam turbines, gas turbines, and other types of turbines. The oil is critical in providing lubrication, cooling, and preventing rust and corrosion in the turbine’s moving parts. Over time, turbine oil can become contaminated with water, dirt, sludge, oxidation products, and wear particles, which degrade its effectiveness. The purification process helps to remove these contaminants, ensuring that the oil retains its performance properties and extends the life of the turbine.
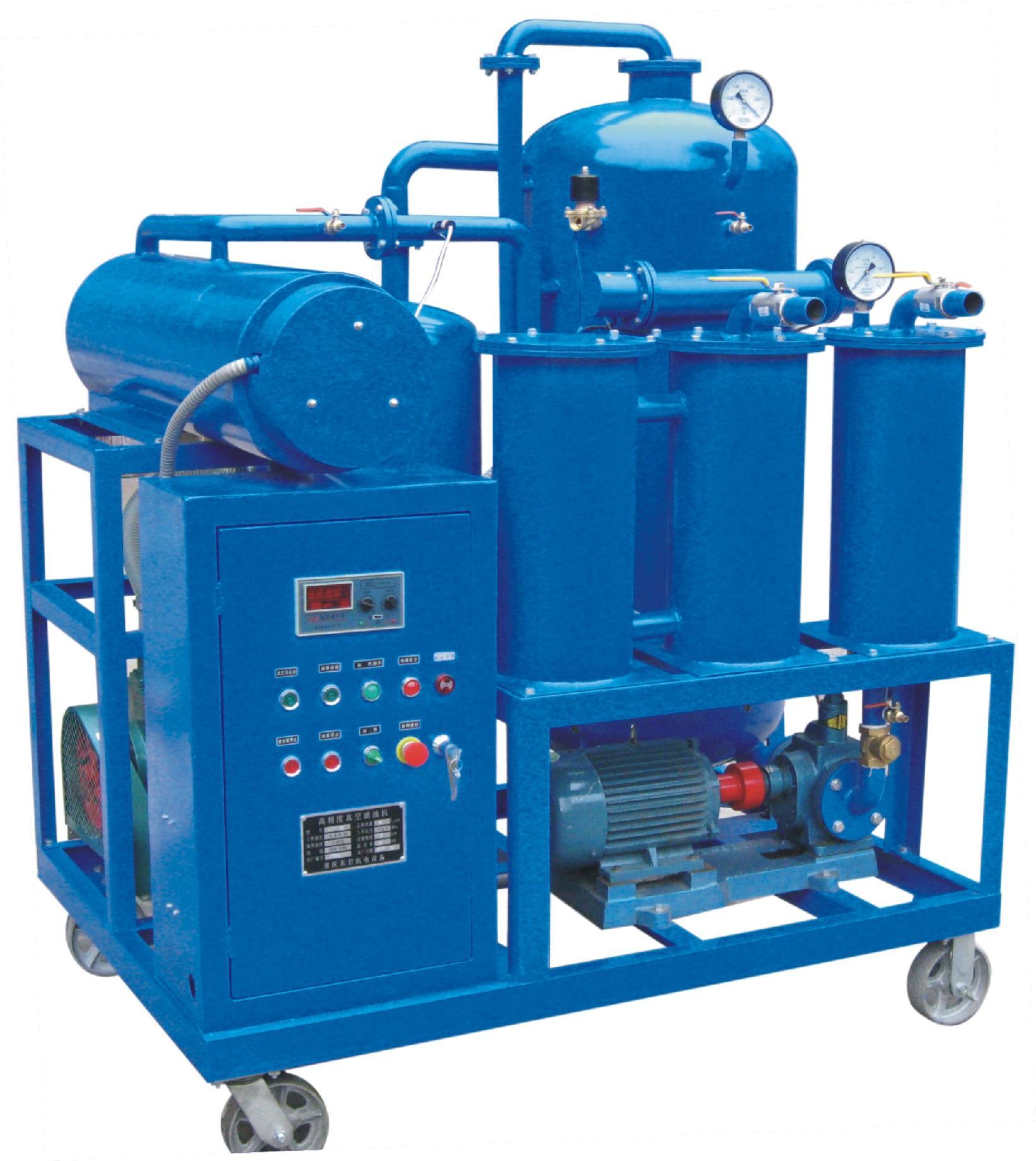
Steps in the Turbine Oil Purification Process:
1. Oil Filtration (Particulate Removal)
- Purpose: Remove large and fine solid particles, such as dirt, dust, metal shavings, and other contaminants from the oil.
- Process:
- The oil passes through mechanical filtration systems, such as paper filters, mesh filters, or cartridge filters.
- Filters with varying mesh sizes are typically used to remove particles of different sizes, starting with larger debris and then moving to finer particulates.
- Some filtration systems may use magnetic filters to capture ferrous (metallic) particles generated by wear or corrosion of turbine components.
Types of filters:
- Coarse filters (for large particles)
- Fine filters (for smaller, finer particulates)
- Magnetic filters (for ferrous metal debris)
2. Dehydration (Water Removal)
- Purpose: Remove water, which can degrade the oil’s performance, lead to corrosion, and cause foaming in the turbine.
- Process:
- Vacuum dehydration is the most common method used. The oil is heated to a specific temperature (usually 60–80°C) and then placed in a vacuum chamber. This reduces the boiling point of water, allowing it to evaporate and be extracted from the oil.
- Centrifugal separation can also be used to remove free water. The oil is subjected to high-speed rotation in a centrifuge, where the water (being denser) is separated from the oil and drained off.
- Silica gel or molecular sieves may be used to absorb any residual moisture that remains in the oil after vacuum dehydration.
3. Degasification (Gas Removal)
- Purpose: Remove dissolved gases such as hydrogen, methane, carbon dioxide, and other volatile compounds that can be generated during the operation of turbines or from oil degradation.
- Process:
- The oil is heated in a vacuum chamber to release dissolved gases, which are then evacuated from the system.
- Removing dissolved gases helps restore the oil's dielectric strength and prevents the formation of gas bubbles, which could lead to cavitation or other operational issues in the turbine.
4. Acid Removal (Deacidification)
- Purpose: Neutralize acids formed due to the oxidation of oil during operation. These acids can cause corrosion in the turbine and degrade the oil's lubricating properties.
- Process:
- Chemical neutralization involves adding a neutralizing agent (such as sodium hydroxide or caustic soda) to the oil to neutralize the acids.
- Activated clay or Fuller’s Earth treatment can also be used to adsorb acidic compounds and oxidation products. The oil is passed through a bed of activated clay, which adsorbs impurities like acids and other polar substances, improving the oil’s quality.
5. Oil Regeneration (Optional, For Heavily Contaminated Oil)
- Purpose: Revitalize highly degraded oil by removing oxidation products and restoring its chemical properties.
- Process:
- Fuller’s Earth or activated carbon can be used to regenerate the oil, especially if the oil is old or has undergone significant degradation.
- The process involves passing the oil through a layer of regenerative material, which adsorbs oxidation by-products, metals, and other contaminants. This helps restore the oil's original characteristics.
6. Fine Polishing (Final Filtration)
- Purpose: Remove any remaining fine particles, contaminants, and degradation products from the oil, ensuring it is clean and clear.
- Process:
- The oil is passed through polishing filters, such as activated carbon filters, diatomaceous earth filters, or fine paper filters to remove residual impurities and improve the appearance and quality of the oil.
- This step helps ensure that the oil is free from any trace contaminants that could impact turbine performance.
7. Final Oil Testing and Quality Control
- Purpose: Ensure the purified oil meets the required specifications and standards for use in turbines.
- Process:
- Breakdown voltage is tested to assess the oil’s insulating properties.
- Moisture content is tested to ensure that the water content is below acceptable levels (typically less than 50 ppm).
- Acidity testing to ensure that the oil’s acidity is within acceptable limits (typically under 0.03 mg KOH/g).
- Gas analysis to check for dissolved gases and confirm their removal.
- Flash point testing to ensure the oil is safe to use and does not present a fire hazard.
- Viscosity testing to ensure the oil maintains proper lubricating characteristics.
After passing these tests, the purified oil is ready to be returned to the turbine or stored for future use.
Equipment Commonly Used in Turbine Oil Purification:
- Vacuum Dehydrators: For removing water and dissolved gases.
- Centrifuges: For separating free water from oil and removing large contaminants.
- Filtration Units: For particulate removal (mesh filters, cartridge filters, etc.).
- Fuller’s Earth Regenerators: For oil regeneration and acid removal.
- Activated Carbon Filters: For final polishing and contaminant removal.
- Polishing Filters: For fine filtration of any residual particulates.
Methods for Turbine Oil Purification:
- Offline (Static) Systems: The oil is drained from the turbine and treated in a dedicated offline system. This is the most common method for routine maintenance and oil changes.
- Online (Dynamic) Systems: These systems treat the oil while it is still in the turbine, allowing continuous operation without the need to remove the oil. Online systems are typically used in large-scale operations where oil quality is monitored continuously.
Environmental Considerations:
- Waste Disposal: The waste products from oil purification (e.g., sludge, used filters, spent chemicals) must be disposed of in accordance with local environmental regulations.
- Recycling: After purification, the oil can be reused in the turbine, reducing the need for new oil and promoting sustainability.
By regularly purifying turbine oil, operators can maintain the oil’s properties, extend the life of the turbine, and prevent costly repairs or breakdowns.