Oil treatment plants for transformers are specialized facilities designed to purify, filter, and maintain the a dielectric oil used in electrical transformers. The primary purpose of transformer oil is to insulate and cool the transformer. Over time, transformer oil can become contaminated with moisture, gases, and particles, or degraded due to oxidation or heat, which can negatively affect transformer performance. Oil treatment plants are used to restore the oil to its original properties and extend the transformer’s operational life.
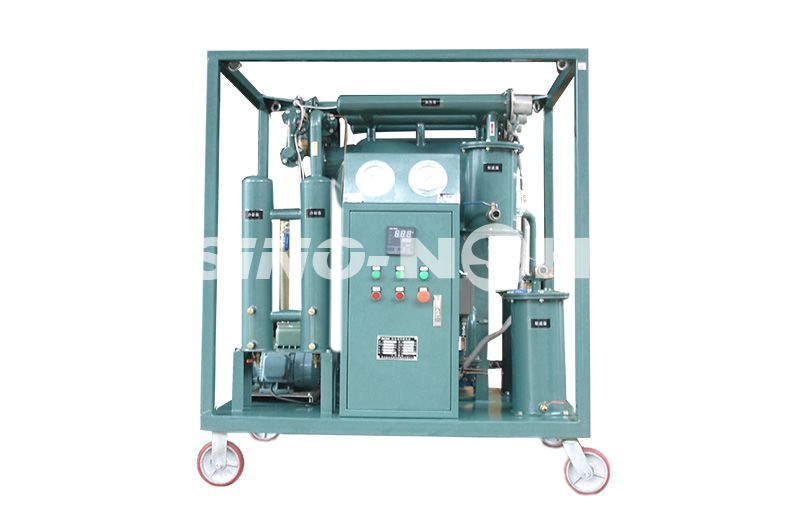
The main types of oil treatment plants and technologies used in transformer oil treatment:
1. Filtration and Degassing Systems
- Purpose: These systems are used to remove particulate contaminants, dissolved gases, and moisture from transformer oil.
- Process:
- Filtration: Involves passing the oil through various filters (e.g., coalescing filters, mechanical filters) to remove solid particles and larger contaminants.
- Degassing: Dissolved gases such as hydrogen, methane, and carbon dioxide are removed by vacuum degassing or by using a combination of heat and vacuum to drive off these gases.
- Moisture Removal: Moisture, which can cause dielectric breakdown, is typically removed using adsorbents or vacuum dehydration.
- Technology:
- Vacuum Dehydration Systems: Heat and vacuum are applied to the oil to remove water and gases.
- Coalescer Filters: These filters facilitate the separation of water and fine particles from the oil.
- Applications: Used for maintaining the quality of oil in transformers in-service or after oil filling.
2. Oil Filtration Units
- Purpose: To filter and purify transformer oil to remove dirt, sludge, and other contaminants.
- Process:
- The oil is passed through several stages of filtration:
- Pre-filtration: Removes coarse particles.
- Fine filtration: Uses finer filters to remove smaller particles.
- Adsorption: Activated carbon or other adsorbents may be used to trap dissolved impurities.
- Technology:
- Portable Oil Filtration Units: These mobile units are used for on-site oil filtration and maintenance of transformers.
- Automatic Filtration Systems: These systems filter oil continuously without manual intervention.
- Applications: Used during routine maintenance or when there is a need to clean the oil without removing the transformer from service.
3. Transformer Oil Regeneration
- Purpose: To regenerate and restore the dielectric properties of the oil.
- Process:
- Regeneration is typically done when the transformer oil has been significantly degraded due to oxidation, aging, or contamination.
- Adsorption Regeneration: The oil is passed through adsorbents (e.g., fuller's earth, activated clay) which remove oxidation products and other dissolved contaminants.
- Vacuum Regeneration: A vacuum is applied to strip dissolved gases, water, and oxidation products from the oil.
- Technology:
- Clay Filtration or Fuller's Earth Treatment: A method where transformer oil is treated with clay or an adsorbent to remove acidic components, sludge, and oxidation by-products.
- Molecular Sieve or Activated Carbon: Used to remove dissolved gases and polar compounds from the oil.
- Applications: Typically used for transformers with highly degraded oil that cannot be purified by simple filtration.
4. Dehydration Systems
- Purpose: To remove moisture from transformer oil, which is critical for maintaining the insulating properties of the oil.
- Process:
- Vacuum Dehydration: Water is removed by applying heat and vacuum to the oil, causing the water to evaporate.
- Heat Treatment: Oil is heated under controlled conditions to help evaporate water and improve oil quality.
- Silica Gel or Molecular Sieve Drying: Adsorbent materials are used to absorb moisture from the oil.
- Technology:
- Vacuum Dehydrators: These are commonly used in oil treatment plants to remove moisture from transformer oil in large quantities.
- Desiccant Drying Units: Units equipped with silica gel or molecular sieves for drying transformer oil.
- Applications: Used to restore the dielectric strength of oil that has absorbed moisture due to leakage, aging, or external contamination.
5. Acid Neutralization
- Purpose: To neutralize the acidic components that develop in transformer oil due to oxidation and aging.
- Process:
- Neutralizing Agents: Chemicals such as alkaline earth metals or other neutralizing agents are introduced into the oil to neutralize acidic compounds.
- Filtration: After neutralization, the oil is filtered to remove sludge and residual neutralizing agents.
- Technology:
- Alkaline Earth Metal Additives: These additives help to neutralize acids formed by oxidation and aging.
- Vacuum and Filter Regeneration: A combination of vacuum dehydration and filtering is used to remove neutralized sludge and oxidation by-products.
- Applications: Used for transformers where oil has become acidic over time, typically due to heat, oxidation, or contamination.
6. Oil Purification Systems (Electrostatic Purification)
- Purpose: To remove very fine particles and dissolved impurities from transformer oil.
- Process:
- Electrostatic Coalescence: An electrical field is applied to transformer oil, causing fine oil droplets to coalesce into larger droplets, which then separate by gravity.
- Technology:
- Electrostatic Oil Purifiers: These systems use an electrostatic field to separate out fine particulate matter and moisture.
- Applications: Used for high-efficiency purification, especially when oil has a high concentration of fine contaminants.
7. Transformer Oil Vacuum Filling Units
- Purpose: To refill transformers with purified or fresh oil, ensuring minimal moisture and air contamination during the process.
- Process:
- Vacuum Filling: The oil is heated, degassed, and filtered before being pumped into the transformer under vacuum to avoid introducing air or moisture.
- Technology:
- Vacuum Oil Filling Units: These units allow for the controlled filling of transformer tanks, ensuring the oil is introduced under a vacuum to prevent contamination.
- Applications: Used during new transformer installations, oil replacement, or major maintenance activities.
8. Gas Separation and Dissolved Gas Analysis (DGA)
- Purpose: To monitor and remove dissolved gases from transformer oil.
- Process:
- Gas Analysis: Regular analysis of the dissolved gases in transformer oil can indicate the presence of issues such as overheating or arcing.
- Gas Separation: If high levels of gases like acetylene, methane, or ethylene are detected, oil treatment plants may use systems to separate these gases from the oil.
- Technology:
- Dissolved Gas Analysis Units: Equipment that continuously monitors the levels of gases in transformer oil.
- Gas Stripping Units: Used to remove dissolved gases from the oil.
- Applications: Used for transformer health monitoring and to prevent failures due to gas buildup.
Conclusion:
Transformer oil treatment plants use a variety of technologies to ensure the oil remains in optimal condition for insulation and cooling. Regular oil treatment is essential for maintaining transformer performance, reducing the risk of failures, and extending the lifespan of the equipment. Depending on the level of contamination, different treatment technologies may be used in combination, including filtration, dehydration, regeneration, and degassing.