The transformer oil treatment procedure is essential for maintaining the insulating properties of the oil and ensuring the proper functioning of the transformer. Over time, transformer oil can accumulate contaminants like moisture, dissolved gases, and solid particles, which can degrade its performance. A thorough oil treatment procedure will help restore the oil’s quality, extend the life of the transformer, and improve overall reliability.
Here’s a step-by-step guide to the typical transformer oil treatment procedure:
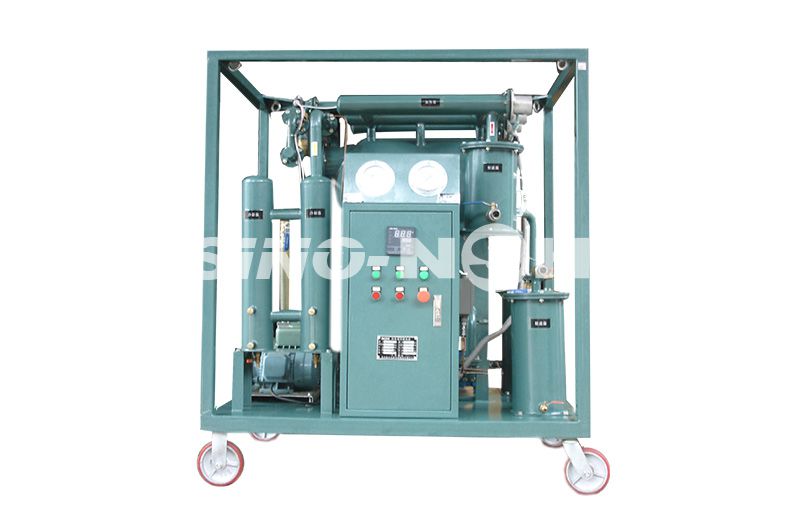
1. Initial Inspection and Analysis
- Sampling: Before starting any treatment, collect a sample of the transformer oil for laboratory analysis. This helps to understand the condition of the oil, such as its acidity, moisture content, and the presence of dissolved gases.
- Visual Inspection: Check the oil for discoloration, opacity, or sediment. These visual indicators can give insight into the oil’s condition.
- Gas Analysis: Identify the gases dissolved in the oil (such as hydrogen, methane, carbon monoxide), which could indicate internal transformer faults.
- Dielectric Strength: Measure the dielectric strength of the oil. This helps in evaluating the oil’s insulating capacity.
2. Oil Dehydration (Moisture Removal)
- Vacuum Dehydration: Using a vacuum transformer oil purifier, the oil is exposed to a high vacuum. The low-pressure environment causes the moisture in the oil to evaporate, as its boiling point is reduced under vacuum.
- Heat Application: In some systems, gentle heating is applied to aid in moisture evaporation without damaging the oil.
- Collection of Moisture: The moisture-laden vapor is then condensed and collected in a separate compartment, leaving the oil much drier.
3. Filtration (Particle Removal)
- Filtration: The oil is passed through a series of filters (e.g., mesh filters, fine filters, and adsorbent filters) to remove any solid particulates, dirt, dust, and other contaminants.
- Deep Filtration: For better filtration, deep bed filtration systems (e.g., using activated charcoal or clay) may be used, which can also help in removing sludge and other impurities.
4. Degasification (Gas Removal)
- Vacuum Degasification: After dehydration, the oil is subjected to further vacuum treatment to remove dissolved gases, including oxygen, nitrogen, and carbon dioxide, which can impair the insulating properties of the oil.
- Pressure Cycling: Some advanced systems use pressure cycling to help release gases trapped in the oil.
- Monitoring Gas Content: Regular monitoring of gas content ensures that gases are properly removed during this stage.
5. Oil Regeneration (Optional)
- Chemical Treatment (Regeneration): In some cases, transformer oil may undergo chemical treatment to neutralize acidity, remove oxidation products, and improve the oil's quality.
- Activated Clay or Silica Gel: These adsorbents are commonly used to remove oxidation byproducts and other impurities from the oil.
- Alkaline Treatment: If the oil is highly acidic, alkaline treatments may be used to neutralize acid content.
- Deodorizing: Some systems also help remove unwanted odors caused by contaminants in the oil.
6. Oil Blending (If Needed)
- If the oil has been heavily degraded or contaminated, it may be necessary to blend fresh oil with the existing oil to bring it up to the required specifications.
- Blending Ratio: This should be done carefully, maintaining the correct ratio of old to new oil to ensure optimal performance.
7. Dielectric Strength Testing
- After treatment, the oil's dielectric strength is tested again to ensure it meets the minimum required standards for insulating effectiveness.
- If the dielectric strength is still below the required value, further treatment may be necessary.
8. Final Filtration and Polishing
- The treated oil may undergo a final polishing phase to remove any fine impurities that could still affect its quality.
- This ensures the oil is as clean as possible before it is returned to the transformer.
9. Recharging the Transformer
- Once the oil treatment process is complete, the purified and conditioned oil is pumped back into the transformer.
- Vacuum Fill: The transformer may be placed under a vacuum to ensure that no air enters during the refilling process, preserving the oil’s quality.
- Final Checks: After the oil is added, perform a final inspection to ensure the oil level is correct and the transformer is free of leaks.
10. Post-Treatment Testing
- Quality Assurance: Perform a final round of tests, including dielectric strength, moisture content, and gas content, to confirm the oil meets the required standards.
- Monitoring: Periodic monitoring should be planned to ensure that the oil continues to perform well and no new contaminants accumulate.
Conclusion
The process of transformer oil treatment involves a combination of dehydration, filtration, degasification, and optional regeneration to restore the oil to optimal conditions. The procedure is aimed at improving the dielectric strength, removing contaminants, and ensuring the long-term reliability of the transformer. Depending on the oil condition and the system's design, the treatment process can vary in complexity, but the core steps outlined above remain standard.