Regular maintenance of a vacuum dehydration oil purification system is essential to ensure optimal performance and extend the lifespan of the equipment. These systems are typically used to remove water and dissolved gases from insulating oils, lubricating oils, or other oils, which improves their performance and reliability.
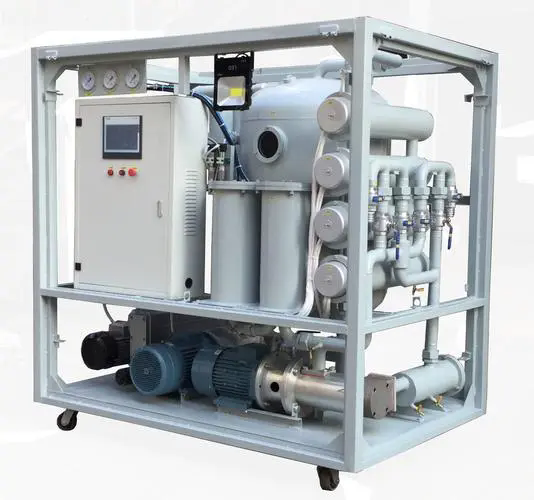
This is a guide for daily maintenance:
1. Check Oil Levels
- Oil Reservoir: Check the oil level in the system's reservoir to ensure it is within the recommended range. If the oil level is too low, top it up with the recommended type of oil.
- Visual Inspection: Inspect the oil for any signs of contamination (e.g., water or particulates). If the oil looks milky or cloudy, it may need to be replaced or filtered further.
2. Monitor System Pressure
- Vacuum Pump Pressure: Check the vacuum pump's operating pressure regularly to ensure it’s within the specified range for efficient dehydration.
- Operating Pressure: The system should maintain a stable vacuum pressure (typically in the range of -0.7 to -0.9 bar). A drop in pressure can indicate a leak or blockage in the system.
3. Check for Leaks
- Vacuum Leaks: Inspect all seals, hoses, and joints for any vacuum leaks. Any leak can reduce the efficiency of the system.
- Tightening Connections: Ensure that all connections and fittings are properly tightened, as loose connections can lead to loss of vacuum or contamination.
4. Inspect the Oil Filter
- Filter Condition: Check the condition of the oil filters. If they appear dirty or clogged, clean or replace them as needed to ensure proper filtration.
- Filter Bypass Valve: Ensure that the filter bypass valve is functioning properly, as it will prevent oil from circulating through the filter if it becomes blocked.
5. Monitor and Clean the Vacuum Pump
- Pump Inspection: Check the vacuum pump for smooth operation. Listen for unusual sounds that could indicate wear or malfunction.
- Pump Oil Change: If the vacuum pump has an oil chamber, ensure that the pump oil is clean and at the correct level. Change the oil at the recommended intervals or as per the manufacturer's guidelines.
- Clean the Pump: Regularly clean the pump's air inlet and exhaust ports to prevent any build-up of dirt or debris.
6. Check Dehydration and Degassing Performance
- Water Removal Rate: Monitor the rate at which water is being removed from the oil. This can typically be seen through a moisture meter or visual inspection of the moisture content in the collected water.
- Gas Purging: Ensure the degassing function is operating correctly. Check if gas bubbles are being efficiently removed from the oil.
- Vacuum Chamber: Inspect the vacuum chamber to ensure no contaminants or sludge are accumulating, which could reduce the system's efficiency.
7. Clean and Inspect the Condenser
- Condensation System: Clean the condenser regularly to ensure it effectively condenses vaporized moisture from the oil. The condensation system can become clogged with residue or scale over time.
- Inspect for Blockages: Check for any blockages in the condensation pipes or cooling system, which could affect the system's overall dehydration capacity.
8. Inspect and Test the Control Panel
- Control Panel Functions: Check that all the control panel indicators and alarms are functioning properly. Ensure that all sensors are working, and that there are no error messages or malfunctions.
- Temperature and Humidity Readings: Regularly monitor and record the temperature and humidity levels to make sure they are within the recommended range for optimal operation.
9. Drain Collected Water and Contaminants
- Water Collection Tank: Regularly empty the water collection tank where the separated water accumulates. If left unemptied, water can mix back with the purified oil, reducing the system’s effectiveness.
- Clean the Tank: After draining, clean the tank to prevent any build-up of residue or contaminants.
10. General Cleaning
- Clean the Exterior: Regularly clean the exterior of the equipment to prevent dust and debris from entering the system. Use a soft cloth or brush to clean around the pump, pipes, and filters.
- Check for Corrosion: Check for any signs of rust or corrosion on external parts. If any are found, treat the surfaces with anti-corrosion compounds.
11. Documentation and Record-Keeping
- Log Maintenance Activities: Keep a detailed log of daily maintenance activities, including oil levels, pressure readings, and any parts replaced. This will help track the system’s performance over time and ensure timely repairs.
Tips:
- Follow Manufacturer’s Guidelines: Always refer to the manufacturer’s manual for specific maintenance intervals and procedures for your vacuum dehydration oil purification system.
- Safety First: Always wear appropriate personal protective equipment (PPE), such as gloves and goggles, during maintenance tasks. Additionally, ensure that the system is powered off and properly isolated before performing any service or repairs.
Would you like additional details on any of these maintenance steps or how to troubleshoot common issues with vacuum dehydration systems?