Maintaining a turbine oil purification system is crucial for ensuring the continuous and efficient operation of turbines (gas, steam, or other industrial turbines) while minimizing downtime and operational costs. The primary goal of a turbine oil purification system is to maintain the quality of the oil by removing contaminants like water, particulate matter, and gases, which can affect the performance and lifespan of both the turbine and the oil. Below are the key maintenance steps and practices to keep the turbine oil purification system running at optimal efficiency.
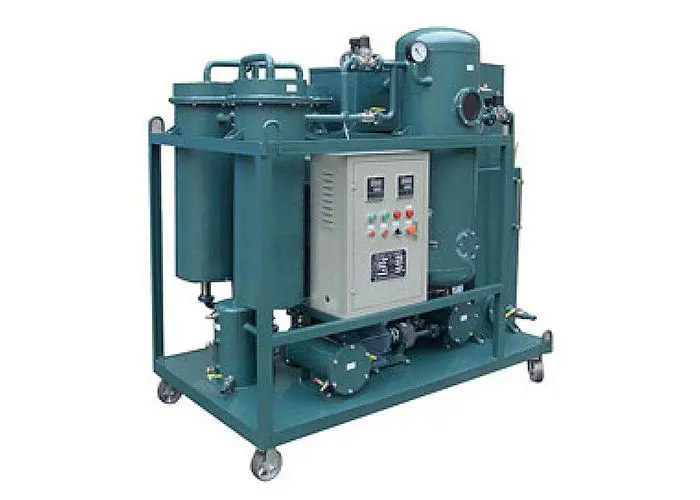
1. Regular Visual Inspections
- System Integrity: Visually inspect the oil purifier unit for any signs of leaks, damage, or wear. Pay particular attention to seals, joints, and connections to ensure that there are no oil leaks.
- Oil Quality: Check the color and clarity of the oil. The oil should be clean and free from any unusual discoloration or cloudy appearance, which may indicate contamination or degradation.
- Filter Inspection: Ensure that the filters are not clogged or dirty. Dirty or blocked filters reduce the efficiency of the purification system and may lead to oil bypass.
2. Routine Cleaning of the Filter Elements
- Check and Clean Filters: Clean the filter elements on a regular basis. If the filters are cleanable (e.g., mesh or coalescing filters), remove them and wash them with appropriate solvents or compressed air to remove contaminants like particulates or sludge.
- replace Disposable Filters: If your system uses disposable filters, replace them as soon as they become saturated or after the recommended number of cycles. Continuing to use a clogged filter can severely reduce the system’s efficiency.
- Pressure Differential Monitoring: Regularly check the pressure differential across the filter. A significant increase in pressure drop across the filter indicates clogging or fouling, signaling that the filter needs cleaning or replacement.
3. Monitoring and Managing Moisture and Water
- Moisture Removal: Turbine oil is sensitive to water contamination, which can cause corrosion, sludge formation, and reduced lubrication properties. Use the water content indicators in the purification system to monitor water levels in the oil.
- Water Separation System Maintenance: Many turbine oil purification systems include dehydration or vacuum dehydration units for moisture removal. Ensure that these systems are working correctly and remove any water trapped in the oil. Periodically check the operation of the moisture removal components, like vacuum pumps and heaters.
- Check for Oil-Emulsion Issues: In some cases, water may emulsify in the oil, making it more difficult to remove. If emulsion is present, you may need to adjust the operation of the water separation process or replace the filtration media.
4. Regular Oil Testing
- Oil Sampling: Periodically take oil samples from various points in the system (e.g., inlet and outlet of the purifier) for laboratory analysis. Test for parameters like moisture content, acidity (TAN – Total Acid Number), particle count, viscosity, and total contaminants.
- Moisture Content Testing: Use specialized equipment like a Karl Fischer titrator to measure the exact moisture content of the oil. Turbine oil should ideally have minimal water content (below 0.1%) for optimal performance.
- Acid Number (TAN) Testing: Regularly check the acid number of the oil. High acidity indicates that the oil has degraded and can cause corrosion of turbine components.
5. Ensure the Correct Operation of Degassing Units
- Gas Removal Efficiency: Many turbine oil purifiers are equipped with degassing units (vacuum or pressure systems) to remove dissolved gases like air, nitrogen, or oxygen. Check that the degassing unit is operating efficiently and maintain it regularly.
- Vacuum Pumps and Filters: In vacuum-based degassing units, monitor the performance of the vacuum pumps and vacuum filters. These parts can wear out over time, and failure may lead to inadequate gas removal.
6. Pump and Motor Maintenance
- Pump Inspection: Turbine oil purifiers rely on pumps to circulate oil through the filtration system. Regularly inspect the pump for signs of wear or damage. Ensure the pump is running at the correct pressure and flow rate for optimal filtration.
- Lubrication and Cooling: Ensure that the pump and motor are properly lubricated, and check for overheating. Overheating of the pump or motor can cause premature failure of the purifier system.
- Motor Inspection: Regularly check the motor for any signs of malfunction, such as unusual vibrations or noises, which could indicate issues with bearings, alignment, or electrical components.
7. Check the Oil Flow Rate and Pressure
- Flow Rate: Monitor the flow rate of the oil through the purification system to ensure it is within the required range for effective filtration. A decrease in flow rate may indicate blockages in the system or filter clogging.
- Pressure Monitoring: Regularly check the operating pressure at different points in the system, especially before and after the filter and degassing units. A drop in pressure could indicate internal blockages or the need for maintenance.
8. Control and Automation System Calibration
- Sensor Calibration: Many turbine oil purification systems are equipped with sensors to monitor oil quality, pressure, temperature, moisture, and flow rate. Calibrate and test these sensors periodically to ensure accurate readings.
- Control Panel Inspection: Inspect the control panel and automated systems regularly. Ensure that alarm settings for critical parameters (e.g., pressure drop, moisture level) are working correctly.
- Automation Systems: If the system has an automated shutdown or alert feature for conditions like high moisture content or low oil flow, verify that these systems are functioning as intended.
9. Seals, Gaskets, and Valves Maintenance
- replace Worn Seals and Gaskets: Over time, seals and gaskets in the purification system can degrade due to exposure to oil and high temperatures. Inspect seals, O-rings, and gaskets for signs of wear and replace them as necessary.
- Check Valves for Leaks: Ensure that all valves in the system are functioning properly and are free from leaks. Leaking valves can compromise the performance of the oil purifier and lead to oil loss.
10. Maintain the Purification System’s Sludge Collection
- Sludge Removal: Many turbine oil purification systems include a sludge collection tank to gather particles and contaminants removed from the oil. Periodically remove the sludge from the tank to prevent overflow or accumulation, which can reduce system efficiency.
- Tank Cleaning: Regularly clean the sludge collection tank to prevent the buildup of hardened sludge, which can affect the overall performance of the purifier.
11. Training and Operator Awareness
- Operator Training: Ensure that personnel operating and maintaining the turbine oil purifier are properly trained. They should understand how to monitor the system, interpret alarms, and perform basic troubleshooting.
- Record Maintenance Activities: Maintain a log of all maintenance activities, including inspections, filter changes, oil analysis results, and repairs. This helps track performance trends and anticipate potential problems.
12. System Shutdown and Major Maintenance
- Periodic Shutdowns for Deep Cleaning: Depending on the operating hours and system usage, periodically schedule a complete shutdown for deep cleaning and inspection of the system. This is an opportunity to check and replace internal components, clean tanks, inspect the pumps, and replace any worn-out parts.
- Major Overhaul: In some cases, an annual or bi-annual overhaul of the entire system may be necessary. This includes replacing major components (like motors, pumps, and filters) that have reached the end of their useful life.
Conclusion
Routine maintenance of a turbine oil purification system is essential for maximizing the life of both the turbine and the oil. By following these practices—regular inspections, cleaning, testing, and monitoring—you can ensure the system operates at peak performance, reduces wear on turbine components and avoids costly downtime.
Would you like to know more about specific tools or methods for testing oil quality or purification efficiency?