An industrial decanter centrifuge is a type of centrifuge used in industrial applications to separate solid particles from liquids or to separate two immiscible liquids with different densities. It achieves this separation by spinning a mixture at high speeds, using centrifugal force to accelerate the process of separation. The solid particles or denser liquid are pushed to the outer part of the centrifuge, while the lighter liquid phase remains in the center.
Decanter centrifuges are used in a variety of industries where liquid-solid or liquid-liquid separation is necessary, including food and beverage, oil and gas, chemicals, wastewater treatment, mining, and pharmaceuticals.
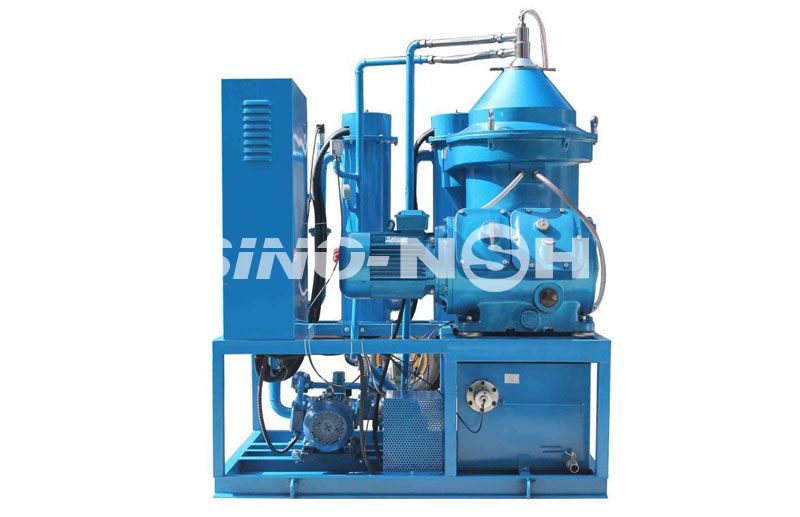
Key Components:
- Rotating Bowl: The central component of the decanter centrifuge, where the separation takes place. It spins at high speeds to generate centrifugal force.
- Screw Conveyor: A helical conveyor located inside the bowl. It moves the separated solid particles to the discharge end of the centrifuge.
- Liquid Discharge Ports: These ports are located at the opposite ends of the centrifuge and allow the clarified liquid (or lighter phase) to exit the centrifuge.
- Solids Discharge Port: At the end of the bowl, the screw conveyor helps push the separated solids toward the solids discharge port.
- Drive System: This system controls the speed of the bowl and screw conveyor to ensure optimal separation.
- Feed Inlet: Where the mixture of liquid and solids (or immiscible liquids) is introduced into the centrifuge.
Working Principle:
The decanter centrifuge operates based on the principle of centrifugal force:
- Feed Introduction: The mixture (containing both solids and liquids or immiscible liquids) is fed into the centrifuge’s rotating bowl.
- Centrifugal Separation: As the bowl spins at high speeds, the centrifugal force separates the heavier particles (solids) or the denser liquid from the lighter phase (the liquid).
- In the case of a solid-liquid separation, the solids are forced to the outer edge of the bowl.
- In the case of liquid-liquid separation, the denser liquid (e.g., oil or water) will form a layer on the outside, and the lighter liquid phase (e.g., oil and water) will separate.
- Solids Discharge: The screw conveyor moves the separated solids toward the discharge port.
- Liquid Discharge: The lighter liquid phase is removed through separate discharge outlets, leaving a clarified liquid behind.
- Continuous Process: Unlike batch centrifuges, decanter centrifuges typically operate continuously, meaning they can handle large volumes of material over extended periods.
Types of Separation:
- Liquid-Solid Separation: The most common application of decanter centrifuges is the separation of solids from liquids, such as in the treatment of wastewater, sludge, or the processing of oils (e.g., palm oil extraction, olive oil production).
- Example Applications:
- Oil and Gas: Separating drilling fluids from solids.
- Wastewater Treatment: Separating sludge or solids from water.
- Food Processing: Separating juice from pulp (e.g., in the production of fruit juice or vegetable oils).
- Liquid-Liquid Separation: Decanter centrifuges are also used for separating immiscible liquids with different densities, such as in separating oil and water.
- Example Applications:
- Oil Refining: Separation of crude oil or oil-based liquids into their components.
- Chemical Processes: Separation of different liquid phases in chemical manufacturing processes.
Advantages of Industrial Decanter Centrifuges:
- High Capacity: Decanter centrifuges can handle large volumes of liquid, making them suitable for continuous processing in industrial environments.
- Efficiency: The centrifuge's ability to rapidly separate solids and liquids means that the separation process is faster and more efficient than traditional methods (e.g., filtration or settling).
- Fine Solids Separation: Decanter centrifuges are effective at separating very fine solids, down to micrometer levels.
- Continuous Operation: They are ideal for continuous operations, unlike batch-based filtration systems, which require stoppages to reload or empty.
- Low Energy Consumption: Compared to other separation technologies, such as pressure filtration or filtration presses, decanter centrifuges can offer lower energy consumption while still providing high throughput.
- Compact Design: They tend to have a smaller footprint compared to other industrial separation equipment, which is useful for facilities with limited space.
Limitations:
- High Maintenance: Decanter centrifuges require regular maintenance, including monitoring wear and tear of the rotating parts, bearings, and seals, to ensure they continue to operate efficiently.
- Capital Investment: The initial cost of purchasing a decanter centrifuge can be high, depending on the size, capacity, and features.
- Noise and Vibration: The high-speed rotation can generate significant noise and vibrations, which may require noise-reduction measures in the installation area.
- Clogging in Feed: If the feed contains very large solid particles or stringy materials, there may be issues with clogging the system, which can reduce efficiency.
Applications of Industrial Decanter Centrifuge:
Oil and Gas Industry:
- Used to separate solids from drilling fluids (muds) and liquids, thereby keeping the mud clean and allowing it to be reused in the drilling process.
- Separation of oil-water emulsions in refineries and petrochemical plants.
Food Processing:
- Used in the separation of juice from fruit pulp in juice production.
- Extraction of vegetable oils (e.g., palm oil, sunflower oil).
- Separating solids from liquids in dairy and other beverage production.
Wastewater Treatment:
- Sludge dewatering in municipal or industrial wastewater treatment plants.
- Removing suspended solids and reducing the volume of sludge for easier disposal or recycling.
Chemical and Pharmaceutical Industries:
- Separation of fine solids from liquids in chemical manufacturing processes.
- Used in the pharmaceutical industry for separating components in drug production.
Mining and Mineral Processing:
- Used in mineral processing for separating valuable minerals from slurry or in the separation of tailings.
- Used for separating fine particles and water during the extraction of ores.
Conclusion:
An industrial decanter centrifuge is a versatile, high-performance separation device used for liquid-solid and liquid-liquid separation in various industrial processes. It operates continuously, can handle large volumes of material, and is capable of separating even fine solids or immiscible liquids effectively. While the initial cost and maintenance requirements may be high, the benefits of efficient, high-capacity separation make it indispensable in industries such as wastewater treatment, oil & gas, food processing, and chemical manufacturing.