The cost of a turbine oil purification system can vary widely depending on several factors such as the capacity of the system (e.g., liters per hour), the type of filtration and purification technology, the manufacturer, and the specific features required (such as automation, heating elements, and filtration stages). Below is a general price range for various types of turbine oil purification systems:
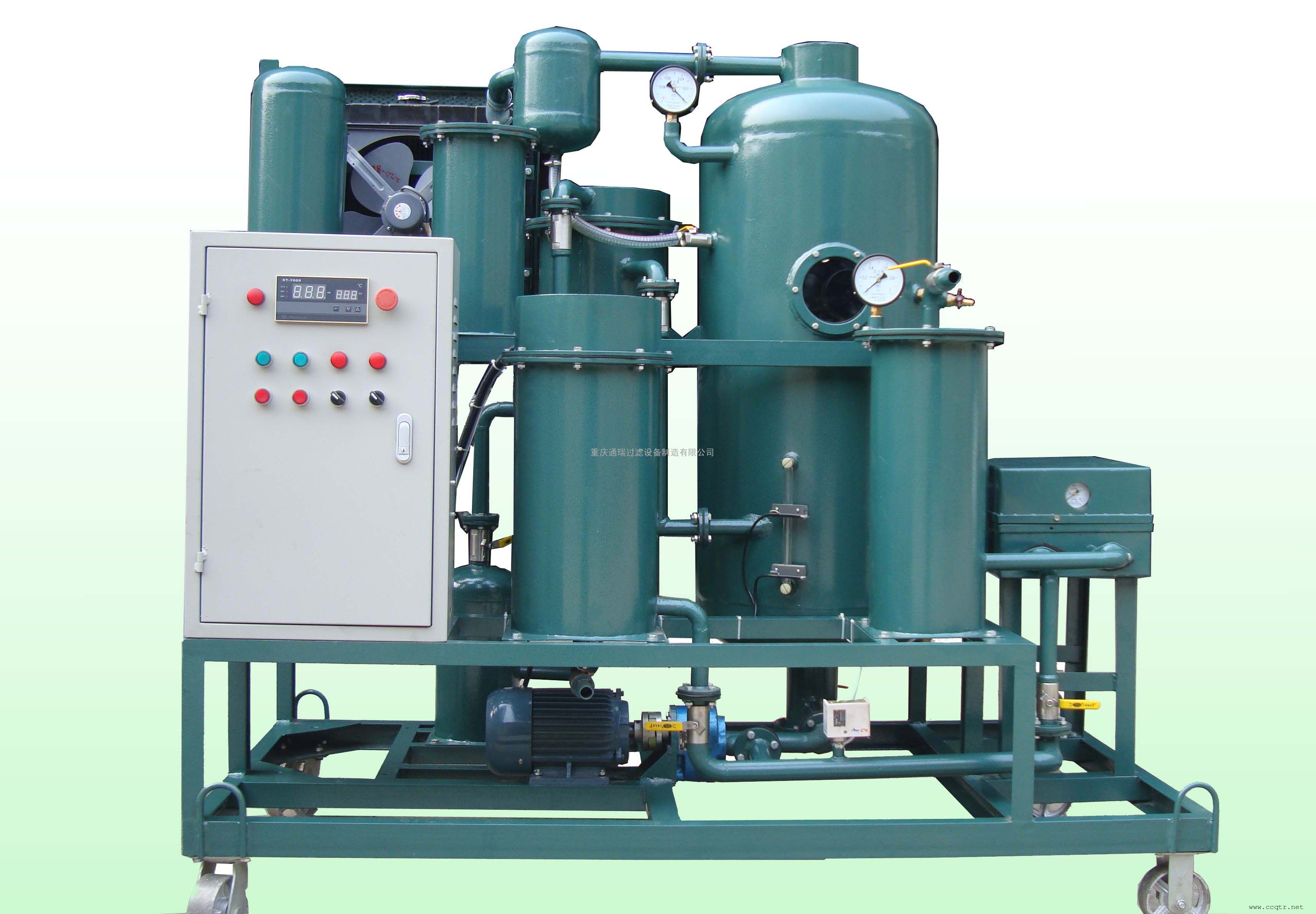
1. Small-Scale Turbine Oil Purification Systems
- Price Range: $5,000 to $30,000 USD
- Capacity: 50 to 200 liters per hour (L/hr)
- Description: These systems are typically used for smaller turbine systems, where less oil is being filtered, and for less demanding applications such as small industrial turbines or smaller power generation units.
- Key Features:
- Single-stage filtration or basic multi-stage filtration.
- Simple vacuum or mechanical filtration systems.
- Basic water and particulate removal.
- Applications: Small power plants, industrial turbines, and backup generators.
2. Medium-Scale Turbine Oil Purification Systems
- Price Range: $30,000 to $100,000 USD
- Capacity: 200 to 1,000 liters per hour (L/hr)
- Description: Medium-sized systems designed for more demanding applications such as medium-sized power plants, turbines in larger industrial facilities, or offshore platforms.
- Key Features:
- Multi-stage filtration with high-efficiency particulate removal.
- Water removal via vacuum dehydration or coalescing.
- Some units include heating for improved oil flow and moisture removal.
- Automated control systems.
- Applications: Larger industrial plants, mid-sized power plants, and offshore turbines.
3. Large-Scale Turbine Oil Purification Systems
- Price Range: $100,000 to $300,000+ USD
- Capacity: 1,000 to 5,000 liters per hour (L/hr)
- Description: High-capacity systems suitable for large power plants, grid-scale turbines, and critical applications where turbine oil needs to be constantly monitored and purified to maintain peak efficiency and prevent failure.
- Key Features:
- Advanced filtration technologies (e.g., molecular sieve, activated carbon).
- Multi-stage systems for particulate filtration, water removal, and oil regeneration.
- High automation with remote monitoring, diagnostics, and real-time condition monitoring.
- Capable of handling highly contaminated or aged turbine oil.
- Applications: Large power plants, high-efficiency industrial turbines, and critical installations.
4. Mobile Turbine Oil Purification Systems
- Price Range: $50,000 to $250,000 USD
- Capacity: 500 to 2,500 liters per hour (L/hr)
- Description: These are portable systems that can be deployed on-site for turbine oil purification in emergency situations or for scheduled maintenance. They are usually trailer- or container-mounted for easy transport and use.
- Key Features:
- Mobile units equipped for full filtration, dehydration, and degassing.
- Designed for field use with integrated heating and pumping systems.
- Often used for turbines in remote locations or for urgent oil purification needs.
- Applications: Offshore platforms, emergency turbine maintenance, remote power stations.
5. Custom and High-End Turbine Oil Purification Systems
- Price Range: $300,000 to $500,000+ USD
- Capacity: 5,000 to 10,000 liters per hour (L/hr) and beyond
- Description: Custom-designed systems for large turbine fleets, high-capacity power plants, or critical infrastructure, where high-efficiency oil purification is essential for ensuring long-term turbine reliability.
- Key Features:
- Multi-stage purification (filtration, dehydration, degassing, and regeneration).
- Cutting-edge technologies for deep purification (e.g., molecular sieves, high-efficiency coalescing filters, and automated monitoring systems).
- Real-time oil analysis, automated controls, and diagnostics for predictive maintenance.
- Customizable for specific turbine brands and oil types.
- Applications: Major power grids, large industrial facilities, and high-efficiency turbine operations.
Key Factors Affecting the Price:
- Capacity: Larger systems capable of handling more liters of oil per hour are significantly more expensive.
- Filtration and Purification Technology:
- Advanced filtration systems (e.g., molecular sieve, activated carbon, coalescing filters) can add to the cost.
- Vacuum dehydration, degassing, and regeneration features are more expensive but increase the system's ability to remove moisture, gases, and particulate contaminants.
- Automation: Systems with advanced automation, remote monitoring, and diagnostics typically have higher costs due to their advanced controls and software.
- Customization: Custom systems designed for specific turbine models (e.g., Siemens, GE, Mitsubishi) or those requiring specialized features will come at a premium.
- Mobility: Mobile systems (i.e., trailer-mounted or skid-mounted) tend to be more expensive because of the added transportability and versatility.
Common Brands and Manufacturers:
- Parker Hannifin
- Evoqua Water Technologies
- Schneider Electric
- Hyundai Oilbank
- Lube Oil Service
- Hering VPT
- Avenew Energy Solutions
- CMM (Messer)
- Rexnord
These manufacturers typically offer a range of systems tailored to different power plant and turbine sizes, as well as offering mobile solutions for on-site oil purification.
Conclusion:
- Smaller systems for low-to-medium capacity turbines typically cost $5,000 to $30,000.
- Medium-sized systems range from $30,000 to $100,000.
- Large, high-capacity systems used in major industrial plants or power stations typically cost $100,000 to $300,000.
- Mobile systems for on-site maintenance are priced between $50,000 to $250,000.
- High-end, custom solutions can cost $300,000 to $500,000 or more, depending on the level of sophistication and capacity.
For accurate pricing, it’s best to consult directly with equipment manufacturers or suppliers, as prices can vary based on the specific features required and the manufacturer's pricing strategy.