The oil-water separation process is a critical operation for purifying lubricating oils, especially when dealing with water contamination. Water can enter lubricating oils through condensation, leakage, or other sources, and if not removed, it can lead to reduced lubrication efficiency, increased wear, corrosion, and even the degradation of oil quality. The process used to separate water from oil depends on the type of contamination (free or emulsified water), the volume of oil, and the purification technology being used.
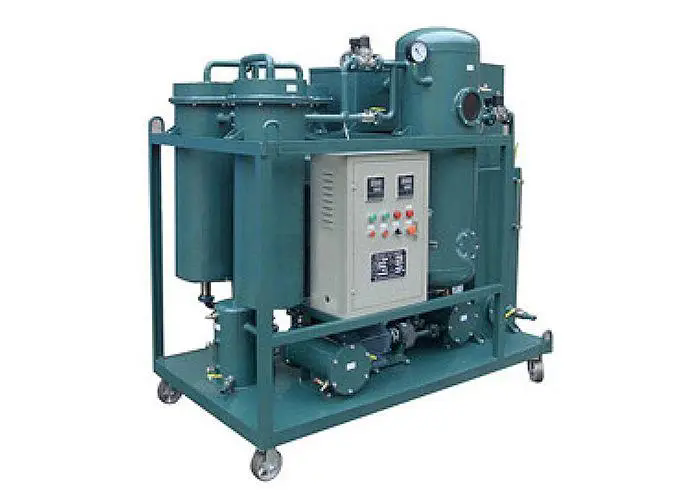
1. Overview of Oil-Water Separation Process
The oil-water separation process generally involves the removal of water in two forms:
- Free water: Water that is not dissolved or emulsified in the oil, but instead exists as droplets or a distinct phase that can be separated more easily.
- Emulsified water: Water that is mixed with oil in tiny droplets, making it more difficult to separate without advanced techniques.
There are several methods and technologies employed in oil-water separation, including physical separation, filtration, and chemical treatments.
2. Separation Methods
A. Gravity Separation (Free Water)
- How it works: This method is based on the difference in density between oil and water. Since water is denser than oil, free water naturally separates and settles at the bottom of the tank, while the oil remains on top.
- Application: This method is best suited for removing free water from the oil, but it may not be effective for emulsified water.
- Process:
- The contaminated oil is allowed to settle in a separator tank.
- Over time, free water collects at the bottom of the tank, and the purified oil floats on top.
- The water is drained off from the bottom, and the oil is recovered.
- Advantages: Simple and low-cost.
- Disadvantages: Ineffective for emulsified water.
B. Coalescing Filtration (Emulsified Water)
- How it works: Coalescing filters are designed to break up emulsions of water droplets suspended in the oil. These filters have materials that cause small water droplets to combine (coalesce) into larger droplets, which can then be separated more easily.
- Application: Primarily used for emulsified water removal.
- Process:
- Contaminated oil flows through a coalescing filter where small water droplets are collected and merged into larger ones.
- These larger droplets then rise to the surface of the oil (if gravity separation is used), or they can be removed using a water collection system.
- Advantages: Efficient at removing emulsified water.
- Disadvantages: Requires filter maintenance and replacement.
C. Vacuum Dehydration (Water Evaporation)
- How it works: Vacuum dehydrators remove both free and emulsified water from oil by lowering the pressure in the system, which causes the water to evaporate at lower temperatures (than normal boiling point).
- Application: Effective for removing both free and emulsified water, especially when the oil is not excessively contaminated.
- Process:
- The contaminated oil is passed through a vacuum chamber where the pressure is reduced.
- Water evaporates at a lower temperature and is collected in a condenser.
- The dehydrated oil exits the vacuum chamber, separated from the water.
- Advantages: Highly effective at removing water without heating the oil to high temperatures, preserving oil quality.
- Disadvantages: Relatively high initial cost and energy consumption.
D. Centrifugal Separation
- How it works: Centrifugal separators use high-speed rotation to apply centrifugal force, which separates water (as well as other contaminants) from the oil based on their differing densities.
- Application: Suitable for removing both free water and solid contaminants.
- Process:
- Contaminated oil is fed into a centrifuge, where it is spun at high speeds.
- The water, which has a higher density, is forced outward and separated from the oil.
- The purified oil exits the centrifuge, while the water is collected and drained off.
- Advantages: Highly effective for separating both free water and solid particulates.
- Disadvantages: Energy-intensive and may not work well for emulsified water.
E. Membrane Filtration
- How it works: Membrane filtration uses semi-permeable membranes to separate water from oil by passing the oil through the membrane, which allows water molecules to pass through while retaining the oil.
- Application: Can be used for both free and emulsified water separation, depending on the type of membrane used.
- Process:
- Oil is forced through a membrane filter, which selectively allows water to pass through while retaining oil molecules.
- The water is removed as permeate, and the purified oil is collected.
- Advantages: Effective at removing very fine contaminants and emulsified water.
- Disadvantages: Requires regular maintenance and cleaning of membranes.
3. Steps Involved in the Oil-Water Separation Process
Regardless of the specific separation technology used, the general steps involved in oil-water separation are as follows:
- Contaminated Oil Collection:
- The oil is collected from the system (e.g., industrial machinery, engine, hydraulic systems) where it is contaminated with water.
- Initial Separation (Optional):
- If there is a large amount of free water, gravity separation or coalescing filtration may be used to remove this initial layer of water.
- Fine Water Removal:
- For emulsified or smaller amounts of water, more advanced methods such as vacuum dehydration, centrifugal separation, or membrane filtration are employed.
- Purification:
- After the water has been removed, the purified oil is filtered again to remove any remaining solids or particulate contaminants.
- Oil Quality Monitoring:
- Throughout the process, it’s essential to monitor the quality of the oil using sensors or sample tests to ensure that the oil is free of contaminants and meets operational standards.
- Storage and Reuse:
- Once purified, the oil is stored or returned to the system for reuse, ensuring optimal lubrication and protection of components.
4. Best Practices for Oil-Water Separation
- Regular Monitoring: Periodically check oil quality to detect early signs of water contamination.
- Preventive Maintenance: Maintain the oil purifier system, including cleaning, changing filters, and ensuring that seals and valves are working correctly to avoid contamination.
- Use of Appropriate Technology: select the right oil-water separation method based on the type and amount of contamination. For example, use vacuum dehydration or coalescing filters for emulsified water, and centrifuges for solid contaminants.
5. Benefits of Effective Oil-Water Separation
- Prolongs Oil Life: By removing water, the oil's lubrication properties are preserved, and its life span is extended.
- Reduces Wear and Tear: Clean oil improves the efficiency and performance of machinery, reducing wear on moving parts.
- Prevents Corrosion: Water can cause rust and corrosion, but by removing it, you protect the metal surfaces of the machinery.
- Enhances Equipment Reliability: Maintaining clean and water-free oil helps to ensure smooth operations, preventing failure and downtime.
In summary, oil-water separation is a crucial process for maintaining the performance and health of machinery and lubrication systems. The selection of the appropriate separation technology depends on the type of water contamination and the specific needs of the application.