Purifying lubricating oil is essential to maintaining its efficiency, extending its life, and ensuring the smooth operation of machinery and engines. Over time, lubricating oil can accumulate impurities such as dirt, water, carbon, oxidation by-products, and metal particles from wear. These contaminants can degrade the oil's lubricating properties, leading to increased wear, corrosion, and potential equipment failure.
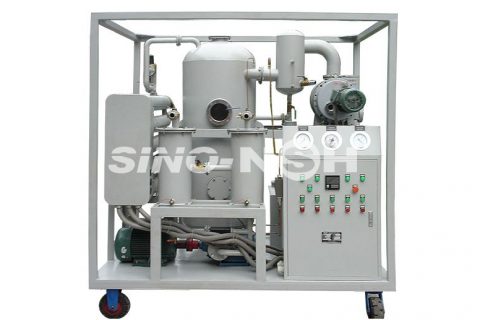
Here’s a comprehensive guide on how to purify used lubricating oil:
Methods of Purifying Lubricating Oil
1. Filtration
- Purpose: To remove solid contaminants such as dirt, soot, carbon particles, and metal debris.
- Method:
- The oil is passed through a filter (e.g., coarse, fine, or micron filters) to capture and remove solid particles.
- Centrifugal filters are also used to separate solid particles from oil through high-speed rotation.
- Equipment:
- Paper filters, mesh filters, or fabric filters can be used for various levels of filtration.
- Benefits:
- Reduces the presence of abrasive particles, preventing wear on moving parts.
- Improves the flow and cleanliness of the oil.
2. Vacuum Dehydration
- Purpose: To remove water (both free and emulsified) from lubricating oil.
- Method:
- The oil is heated and placed in a vacuum chamber where the pressure is reduced, causing water to evaporate at a lower temperature.
- The water vapor is then removed from the oil, restoring its insulating and lubricating properties.
- Benefits:
- Removes moisture, preventing oxidation and corrosion.
- Maintains the oil’s viscosity and reduces foaming.
- Restores the oil’s dielectric strength, especially for electrical insulating oils.
3. Centrifugation
- Purpose: To separate water and solid contaminants from the oil.
- Method:
- The used oil is placed in a centrifuge, where it is spun at high speeds. The centrifugal force separates the heavier particles and water from the oil.
- Water and solid contaminants are forced to the outer wall of the centrifuge and can be removed.
- Benefits:
- Highly effective for removing both water and solid contaminants.
- Suitable for oils with a high level of contamination.
4. Activated Carbon Adsorption
- Purpose: To remove oxidation products, sulfur compounds, and other chemical contaminants from used oil.
- Method:
- The oil is passed through an activated carbon bed, which adsorbs contaminants such as acids, gases, and other organic compounds.
- Activated carbon can remove both dissolved and particulate impurities from the oil.
- Benefits:
- Helps restore the oil’s color, odor, and overall quality.
- Removes acidity and contaminants, preventing oil degradation.
5. Clay Treatment (Clay Filtration)
- Purpose: To remove oxidation products and impurities that affect the oil's performance.
- Method:
- The oil is treated with activated clay, which adsorbs impurities like oxidized compounds, metallic oxides, and carbonaceous matter.
- The oil and clay are mixed, and the treated oil is separated from the clay, which can be regenerated for future use.
- Benefits:
- Restores the oil’s transparency and removes unwanted oxidation by-products.
- Effective in reducing acid numbers and improving the oil’s stability.
6. Chemical Treatment
- Purpose: To neutralize acids formed during oxidation and restore oil properties.
- Method:
- Neutralizing agents (such as alkali compounds or base oils) are added to the oil to neutralize acidic compounds formed by oxidation or degradation.
- Antioxidants may also be added to prevent further degradation.
- Benefits:
- Restores the oil’s pH balance and stops further degradation.
- Improves oxidation resistance and oil stability.
7. Distillation (Re-refining)
- Purpose: To separate volatile contaminants from used lubricating oil and recover high-quality base oil.
- Method:
- The oil is heated in a distillation column where lighter components (such as water and volatile chemicals) are separated from the heavier, valuable base oil.
- This process is typically used in re-refining used oils.
- Benefits:
- Restores oil’s original viscosity by removing volatile contaminants.
- Allows for the recovery of high-quality oil for reuse.
- Reduces the need for new base oil and minimizes waste.
8. Polishing and Additive Blending
- Purpose: To restore the lubricating properties and performance of the oil after purification.
- Method:
- After the filtration and dehydration processes, the purified oil can be polished using fine filters to remove any remaining fine particles or traces of contaminants.
- Additives such as anti-wear agents, rust inhibitors, antioxidants, and detergents can be blended into the oil to restore its anti-corrosion, anti-foaming, and oxidation resistance properties.
- Benefits:
- Restores full lubricating performance to the oil.
- Improves oil life and enhances protection against wear, rust, and oxidation.
Steps for Purifying Used Lubricating Oil:
Pre-Inspection:
- Analyze the oil for contaminants such as water, dirt, and oxidation products, to determine the appropriate purification method.
- Check the viscosity and acid number to assess the level of degradation.
Filtration and Coarse Removal:
- Use coarse filtration to remove large particles and debris from the oil.
Dehydration and Gas Removal:
- Vacuum dehydration or centrifugation to remove moisture and dissolved gases (such as oxygen or nitrogen).
Fine Filtration and Adsorption:
- Activated carbon and clay treatment to remove dissolved contaminants, oxidation by-products, and chemical impurities.
Chemical Treatment (if needed):
- If the oil shows signs of acidity or oxidation, neutralize acids and restore the oil’s properties with additives or alkali agents.
Polishing and Final Testing:
- Use fine filters to polish the oil and ensure it is free of particulate matter.
- Conduct quality testing (viscosity, dielectric strength, acid number) to ensure the oil meets performance standards.
Re-blending and Reconditioning:
- Add additives to the purified oil to restore its performance, such as anti-wear agents, anti-oxidants, or detergents.
Benefits of Lubricating Oil Purification:
- Cost Savings: Reduces the need to purchase new lubricating oil, saving on maintenance costs.
- Environmental Benefits: Reduces the environmental impact of waste oil disposal by reusing and recycling the oil.
- Improved Equipment Performance: Keeps machinery running smoothly by maintaining the integrity of the oil, reducing wear and tear.
- Extended Oil Life: Oil purification significantly extends the life of the lubricating oil, improving equipment uptime.
Purifying lubricating oil involves a combination of physical and chemical processes, including filtration, dehydration, distillation, adsorption, and additive blending. The specific purification method will depend on the type of oil, the level of contamination, and the equipment's requirements. By using these purification methods, you can extend the life of the lubricating oil, reduce maintenance costs, and improve the performance and reliability of machinery.