Choosing the right transformer oil purification equipment is critical for ensuring the efficient operation, longevity, and safety of transformers. The primary goal of oil purification is to remove contaminants (such as water, sludge, and particles) from the transformer oil, maintaining its insulating properties and cooling capacity. Below are the key factors to consider when selecting the appropriate transformer oil purification equipment:
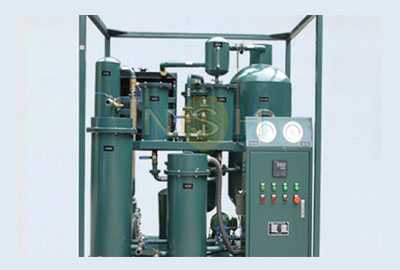
1. Type of Contaminants in the Oil
- Water: One of the most common contaminants in transformer oil, water reduces the oil’s dielectric strength and can lead to transformer failure.
- Sludge and Particulates: Sludge, dirt, and metallic particles can accumulate in the oil over time, which can damage the transformer’s internal components.
- Acids: Oxidation of oil can lead to the formation of acids that degrade the oil and transformer components.
- Gases: Gases can dissolve in the oil or form as a result of electrical faults (e.g., carbon dioxide or hydrogen). While this may not always require immediate purification, the ability to remove dissolved gases may be beneficial.
2. Volume of Oil to Be Purified
- Small Transformers: For small transformers (up to 100 kVA), you might need equipment with a smaller capacity, typically in the range of 200–500 liters per hour.
- Medium Transformers: For transformers in the range of 100 kVA to 5 MVA, look for equipment with a capacity of 500–2,000 liters per hour.
- Large Transformers: For large transformers (5 MVA and above), you'll need high-capacity equipment, capable of handling up to 10,000 liters per hour or more, depending on the size of the transformer and the volume of oil to be purified.
3. Type of Oil Purification Process
Different types of purification systems are available, each suited to different contamination levels and operating conditions. The key methods are:
4. Operating Conditions and Location
- Environment: Consider whether the equipment will be used in a harsh environment, such as outdoor or offshore locations, where factors like weather, humidity, and dust may influence performance.
- Ease of Mobility: If oil purification is needed in various locations or as part of regular transformer maintenance, portable filtration units are preferred.
- Space Constraints: Ensure that the purification equipment fits within the available space and is easy to integrate into your maintenance infrastructure.
5. Filtration Efficiency and Capacity
- Micron Rating: The filtration system’s micron rating determines how small a particle the filter can capture. A typical transformer oil filter has a rating of 1 to 10 microns, ensuring it removes both larger particulates and finer contaminants.
- Flow Rate: The system’s flow rate (measured in liters per minute or gallons per minute) should match the volume of oil to be purified and the required throughput. A higher flow rate is needed for large transformers or urgent maintenance.
Ensure the equipment can handle the oil volume within the necessary time frame, without excessive downtime during filtration.
6. Maintenance and Operating Costs
- Filter Life: Check how often filters need to be replaced or cleaned. Systems with longer filter life or self-cleaning mechanisms can reduce operational costs.
- Energy Consumption: Consider the energy efficiency of the system, particularly if it uses vacuum pumps or motors that may consume significant power. Lower energy consumption helps in reducing the overall cost of operation.
- Ease of Maintenance: Look for equipment that is easy to maintain and repair, with accessible components like filter elements, pump seals, and oil tanks. Systems with built-in diagnostic features can help monitor performance and reduce the risk of system failure.
7. Level of Automation
- Manual vs. Automatic: Some oil purification systems are fully automated, which minimizes human intervention, ensures consistent performance, and reduces the risk of operational errors.
- Control Systems: Advanced systems offer automated control panels with features like pressure and flow rate monitoring, alarms, and automatic shut-off to prevent damage. These systems also allow for remote monitoring and diagnostics.
- Operator Training: Choose equipment that is easy to operate and maintain. For highly automated systems, ensure that operators can be trained quickly.
8. Certification and Compliance
- Quality Standards: Ensure that the oil purifier meets industry standards and certifications such as ISO, IEC, or ASTM to ensure its reliability, safety, and compliance with quality standards.
- Environmental Compliance: Transformer oil purification systems must comply with local environmental regulations for the disposal of waste materials (sludge, water, and oil residues).
9. Manufacturer Reputation and Support
- Manufacturer Experience: Choose a purifier from a reputable manufacturer with experience in transformer oil purification. Ensure they offer reliable customer support and spare parts availability.
- Warranty and Service: Make sure the equipment comes with a solid warranty and that after-sales service is available, including maintenance, repairs, and spare parts.
10. Budget
- Initial Cost: Depending on the type of system (centrifugal, vacuum, combination), the initial cost can vary significantly. Consider the purchase cost within your budget and the expected return on investment.
- Total Cost of Ownership: Include ongoing costs for energy, filter replacement, maintenance, and waste disposal. It is important to calculate the total cost of ownership over the life of the equipment.
Summary of Key Factors to Consider:
Factor | Consideration |
---|
Type of Contaminants | Choose equipment based on the type of contaminants (water, sludge, particulates, acids, gases). |
Volume of Oil | select a purifier with a capacity that matches the size of the transformer and the volume of oil to be purified. |
Purification Method | Decide between centrifugal, vacuum, or clay filtration based on your specific needs (e.g., water removal, sludge). |
Flow Rate and Efficiency | Ensure the purifier can process oil at the required flow rate with the correct filtration micron rating. |
Maintenance Costs | Consider the cost of maintenance, filter replacement, and energy consumption. |
Automation and Control | Automated systems are more efficient, but may cost more upfront. |
Compliance and Certification | Ensure compliance with industry standards and regulations. |
Conclusion:
Choosing the right transformer oil purification equipment depends on the specific needs of your transformers, the type and level of contamination in the oil, and the overall operational and maintenance requirements. It's essential to balance performance, cost, and ease of use to ensure that the equipment effectively maintains oil quality and transformer health over the long term.