Choosing a transformer oil regeneration plant requires careful consideration of several factors to ensure that the system meets your needs, operates efficiently, and maintains the quality of the transformer oil. Transformer oil regeneration is essential for restoring the insulating properties of oil used in transformers, which can degrade over time due to contamination by moisture, sludge, acids, and other impurities. A regeneration plant should efficiently remove these contaminants and restore the oil to a usable condition.
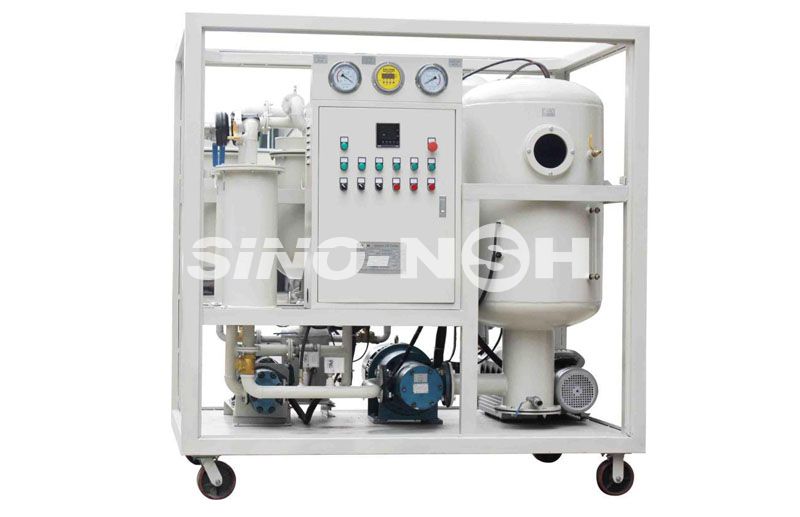
Key Factors to Consider When Choosing a Transformer Oil Regeneration Plant
1. Type of Contamination in the Oil
- Moisture: Water in transformer oil can cause insulation breakdown and reduce dielectric strength.
- Acids and Sludge: Oxidation of the oil leads to the formation of acids and sludge, which reduce oil quality and can damage transformer components.
- Gases: Dissolved gases such as hydrogen and carbon monoxide can accumulate over time, leading to a degradation of the oil.
- Particulate Contamination: The presence of particulate matter, including dirt, metal shavings, or other solid debris, can cause damage to the transformer.
Choice of Regeneration Plant: Different plants are designed for different types of contamination, so identifying the specific contaminants in the oil will help determine the type of plant you need. For example:
- Vacuum Dehydration or Vacuum Oil Purification Systems are great for removing moisture.
- Acid Neutralization and Clay Filtration systems are ideal for removing sludge and neutralizing acids.
- Fine Filtration and De-gassing units can be used for particulate and gas removal.
2. Regeneration Method
Transformer oil regeneration plants employ different technologies for oil purification and regeneration. The main methods include:
Choice of Method: Choose a plant that combines the right regeneration methods for your specific oil contamination. For example, a plant with both vacuum dehydration and clay filtration will handle water and sludge removal efficiently.
3. Oil Volume and Throughput
- The volume of oil you need to process is a critical factor in determining the capacity of the regeneration plant.
- Small-Scale vs. Large-Scale: Choose a plant that can handle the volume of oil you expect to process daily, whether it's for a single transformer or for multiple units in a power plant or substation.
- The plant should be capable of regenerating oil at an optimal rate without compromising the quality of the treated oil.
Consideration: Match the plant's throughput capacity to your expected oil regeneration volume. Plants with a higher throughput tend to have larger filters, tanks, and vacuum systems.
4. Efficiency and Oil Quality Restoration
- A good regeneration plant should be capable of restoring the oil to a high quality that meets the specifications required for transformer operation. This includes restoring the oil’s dielectric strength, moisture content, acid number, and sludge content to acceptable levels.
- Look for plants with continuous monitoring systems to measure the quality of the oil during the regeneration process (e.g., dielectric strength meters, moisture meters, and gas analyzers).
Consideration: Ensure the plant is effective in regenerating the oil back to the original specifications, particularly in terms of dielectric strength and moisture content.
5. Energy Consumption and Operating Costs
- Energy Efficiency: Transformer oil regeneration processes like vacuum dehydration can be energy-intensive. Look for systems that are energy-efficient, have low maintenance costs, and minimize waste.
- Operating Costs: Consider not only the initial purchase cost but also the long-term operating and maintenance costs, including the cost of consumables (such as activated carbon or filter cartridges), energy, and labor.
Consideration: Evaluate the cost-effectiveness of the plant by considering both the initial capital investment and ongoing operational costs.
6. Automation and Control Features
- Automation: Modern transformer oil regeneration plants are equipped with automation features that monitor and control the entire process, ensuring consistent oil quality and reducing the need for manual intervention.
- Control Systems: A plant with an intuitive control system allows operators to monitor parameters such as moisture content, oil temperature, and flow rate.
- Remote Monitoring: Some plants come with remote monitoring capabilities, allowing operators to access real-time data and control the system remotely.
Consideration: Look for a plant with automated controls that are user-friendly and provide real-time data monitoring, alarms, and reporting for better process control.
7. Environmental Impact and Sustainability
- Regeneration plants should be designed with environmental sustainability in mind. Consider whether the plant generates waste that needs to be disposed of (e.g., sludge or spent carbon), and ensure that it complies with environmental regulations.
- The oil regeneration process should minimize environmental risks, particularly when it comes to the disposal of contaminants like used oil and chemicals.
Consideration: Check that the plant meets all relevant environmental standards and is designed to minimize waste and emissions.
8. Maintenance and Service Support
- Choose a regeneration plant from a reputable manufacturer that offers good after-sales service, including installation, training, and maintenance support.
- Consider the availability of spare parts and service contracts to keep the plant running smoothly and reduce downtime.
- Ensure that the plant is easy to maintain with simple cleaning, oil filter replacement, and other routine maintenance tasks.
Consideration: Ensure that the manufacturer offers reliable customer support, and check for service contracts or maintenance agreements to ensure long-term reliability.
9. Regeneration Plant Configuration
- Modular Design: Some regeneration plants come with a modular design that allows for easy scaling. This is especially useful if you expect future increases in oil regeneration needs.
- Turnkey Solutions: Some suppliers offer turnkey solutions, including installation, commissioning, and operator training, which can save time and reduce complexity.
Consideration: If you anticipate growth or need flexibility, a modular plant may be beneficial.
Steps to Choose a Transformer Oil Regeneration Plant
- Assess the contamination level in your oil (moisture, acids, sludge, gases, etc.).
- Match the regeneration method to the type of contamination present.
- Determine the required oil throughput based on the volume of oil you need to process.
- Evaluate the plant's efficiency in restoring oil to acceptable quality standards.
- Compare energy consumption and operating costs against your budget.
- Look for automation features to reduce labor and improve control.
- Ensure the plant complies with environmental regulations and offers sustainable waste disposal methods.
- Check for after-sales support and service contracts.
- Consider future needs and choose a plant that offers scalability and flexibility.
Choosing a transformer oil regeneration plant is a significant decision that requires balancing the specific needs of your operations with the available technology and budget. By considering factors like contamination type, regeneration methods, capacity, efficiency, and ongoing costs, you can select the best solution that will ensure the long-term performance of your transformers while maintaining high environmental and operational standards.