Lubricating oil purifiers can be used for waste oil purification and recycling, though they are typically designed to handle oils used in various machinery, including engines, turbines, compressors, and hydraulic systems, rather than transformer oil specifically. These purifiers can be quite effective in removing contaminants from used lubricating oil, making it suitable for reuse or safe disposal. They are part of a broader category of oil purification and recycling systems, helping to extend the life of the oil and reduce waste.
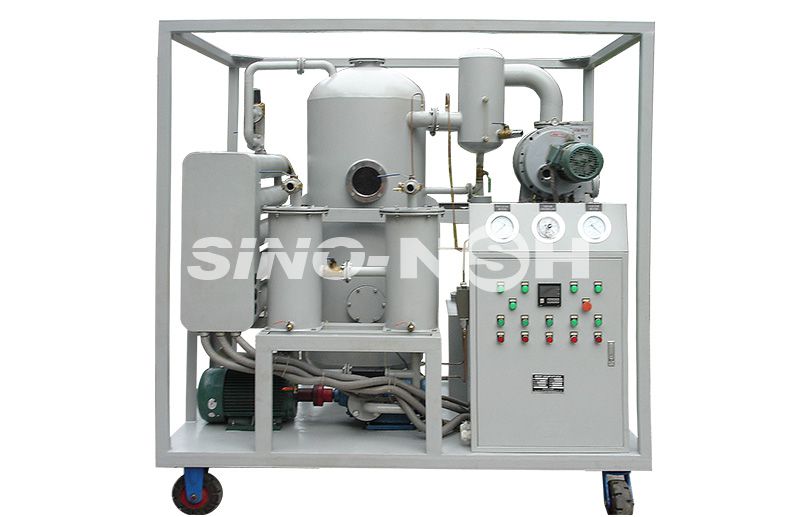
How Lubricating Oil Purifiers Work in Waste Oil Purification and Recycling
Lubricating oil purifiers generally use a combination of physical and chemical processes to clean and recycle waste oil. The processes vary depending on the purifier type, but here are the main ones:
1. Filtration
- Purpose: To remove solid contaminants such as dirt, carbon particles, metal wear debris, and sludge from the used oil.
- Method: The waste oil is passed through various types of filters, such as:
- Coarse filters to catch larger particles.
- Fine filters or micron filters to capture smaller contaminants.
- Filtration is one of the primary methods to maintain the cleanliness of lubricating oil and ensure that it can be safely reused in machines without causing damage.
2. Centrifugation
- Purpose: To remove water, solid particulates, and sludge from the waste oil.
- Method: The oil is subjected to centrifugal forces in a centrifuge, which forces heavier contaminants (such as water, dirt, and sludge) to the outer walls of the bowl. These contaminants can then be removed, leaving cleaner oil.
- Centrifugation is especially useful for removing water and fine particles from waste oils.
3. Dehydration
- Purpose: To remove free water or emulsified water (water that is mixed into the oil).
- Methods:
- Vacuum Dehydration: The oil is heated under a vacuum, lowering the boiling point of water so that it evaporates and can be removed.
- Coalescing: A filter or system that causes small water droplets to combine into larger ones, which can then be separated from the oil.
- Centrifugal Separation: This also helps to remove water by using centrifugal force.
4. Degassing
- Purpose: To remove dissolved gases like oxygen, nitrogen, carbon dioxide, and hydrocarbons from the waste oil. Dissolved gases can degrade oil quality and contribute to oxidation.
- Method: The oil is subjected to vacuum conditions or passed through a degassing unit to remove these gases.
- This is important for preventing the formation of acidic compounds and improving the lubricating properties of the oil.
5. Deacidification and Neutralization
- Purpose: To neutralize acids that form in the oil during use, primarily due to oxidation or chemical reactions with contaminants.
- Method: Alkaline agents or neutralizing chemicals can be added to the oil to bring its pH back to an acceptable level and remove acidic compounds.
- Clay treatment or additives can also be used to remove oxidation by-products from the oil.
6. Activated Carbon Adsorption
- Purpose: To remove dissolved organic compounds, such as oxidation products, sulfur compounds, and other chemical contaminants that can degrade oil quality.
- Method: The oil is passed through a bed of activated carbon, which adsorbs harmful substances, improving the oil’s quality and making it reusable.
7. Re-refining (Advanced Purification)
- Purpose: To re-refine the used lubricating oil, restoring it to a state where it can perform like new oil in machinery.
- Method: This is done by subjecting the oil to a combination of distillation, vacuum treatment, and thermal processes to remove light hydrocarbons, oxidation by-products, and other impurities.
- Re-refining units often involve more complex systems like thermal cracking or distillation to break down and separate contaminants from the oil.
8. Blending and Additives
- After purification, the oil is often blended with fresh oil or additives to restore properties like viscosity, anti-wear characteristics, and oxidative stability.
- Additives might include:
- Anti-oxidants to prevent further degradation.
- Anti-wear agents to protect engine components.
- Rust inhibitors to prevent corrosion.
Additives can be formulated based on the application of the oil (e.g., industrial machinery, automotive engines, or turbines).
9. Quality Control and Testing
- After purification, the treated oil undergoes various tests to ensure it meets required specifications. These tests typically include:
- Viscosity testing to check the flow characteristics.
- Dielectric strength testing (for electrical insulating oils).
- Water content measurement.
- Acid number (neutralization value) to determine the degree of oil acidity.
- Particle count to verify cleanliness.
Benefits of Using a Lubricating Oil Purifier for Waste Oil Recycling:
- Cost Savings: Recycling waste oil significantly reduces the need for purchasing new oil, especially in industries that use large quantities of lubricating oil.
- Environmental Benefits: Proper recycling helps reduce the environmental impact of used oil, which can be harmful if improperly disposed of.
- Improved Equipment Longevity: Recycled oil can provide the same level of protection as new oil, reducing wear on machinery and extending its service life.
- Reduced Disposal Costs: Recycling reduces the need for costly disposal methods for hazardous waste oil.
Lubricating oil purifiers can indeed be used for waste oil purification and recycling, especially in industries where large amounts of lubricating oils are used (e.g., automotive, industrial machinery, power plants, and turbines). These systems typically focus on removing contaminants (such as water, particles, and degradation by-products) and improving the overall quality of the used oil, making it safe for reuse. In this way, purifiers help reduce waste, conserve resources, and minimize the environmental impact associated with oil disposal.